Workflow Optimization – Enhancing the Operational Efficiency of Business Processes
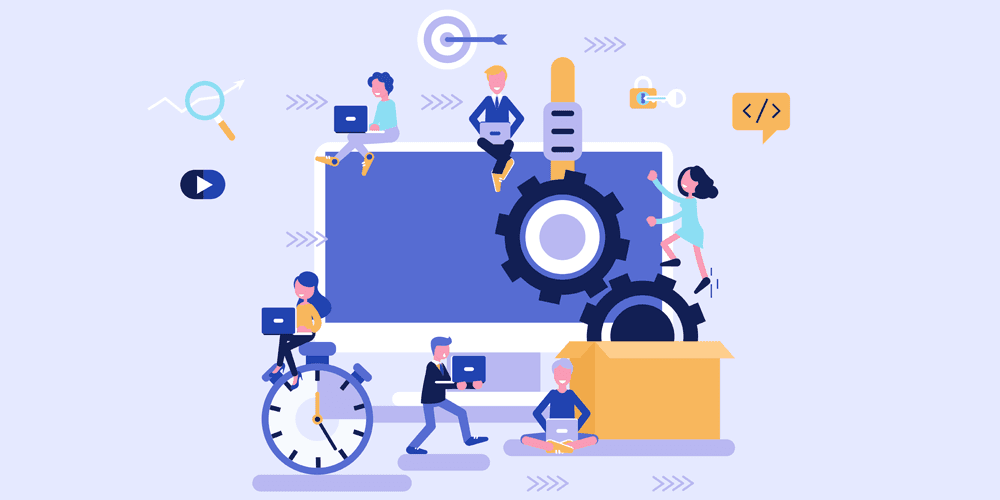
You have created comprehensive workflows and employed the best resources, yet the results are not as expected. Why?
Your workflows need to be reviewed and optimized constantly for operational excellence. Workflow optimization is an essential practice that minimizes waste and increases efficiency.
Workflow optimization must be made part of the business strategy in order to make processes faster, more cost-effective, and streamlined. In this blog, you will learn how to optimize workflows, tested workflow optimization strategies, and ways to optimize workflows.
What is Workflow Optimization?
Workflow optimization is the use of strategies and tactics to improve the efficiency of administrative, industrial, and other processes. Before we get into workflow optimization, it is important to understand when a workflow is. In every organization, two categories of work are carried out – tasks and workflows.
A task is a single assignment that an employee completes and moves into the next one. A workflow is a series of tasks that need to be completed, usually regularly to complete a task.
In small businesses, workflows are mostly linear and simple to understand. As businesses grow, workflows become more complex with branches that create an interconnected web. Vendor relationship management, supply chain management, purchase approval requests, sales prospecting, and customer onboarding are all examples of process workflows.
Workflows are multitasked processes that move and rely on data. There are several types of workflows, some are focused on solving simple problems, while others are more intricate with multi-level issues.
Case workflows are more ambiguous types of workflows that do not have a clear beginning, but have a process to follow for gathering data. Project workflows are made up of systems that help begin the project and guide it to completion. Process workflows are predictable and recurring with systems in place to help them move smoothly from start to finish.
The meaning of workflow optimization is the process of streamlining workflows using automation and integration to connect disparate systems. The result of workflow optimization is a streamlined system for carrying out tasks that eliminate unnecessary human elements, reducing risk, cost, and bottlenecks.
An optimized workflow can scale with business growth. Primarily, workflow optimization looks to reduce manual processing and physical paperwork. Manual processing often means there is no digital copy of a document. Without a digital copy, the accountability or traceability of tasks within the process is also lost. Optimizing a workflow helps businesses track and control their processes for optimal outcomes.
Workflow optimization is all about determining which tasks in a process are most crucial for success, How the process can be improved, which tasks need to be eliminated, and which tasks need to be automated.
Tested Workflow Optimization Strategies
At a high level, workflow optimization aims at increasing the efficiency of business processes. There are several ways in which workflows can be optimized. We have listed below, 7 of the most successful ways of optimizing a workflow. Organizations can review the below strategies to determine how to optimize workflow models for their use case.
1. Agile
Agile workflows are stepwise visual representations of a process workflow that emphasizes interaction, collaboration, and adaptability. These workflows were initially favored by software developers, but have now been adopted by other popular sectors.
Agile workflows help you drive transparency and adaptability to the way processes are executed. These are defined processes for managing projects, completing work, and delivering products and services to clients in every business.
2. Business Process Improvement
business process improvement (BPI) is a method for optimizing workflows by identifying parts of a process that are less efficient and effective. Optimizing processes using BPI techniques makes them error-free and addresses issues continually.
3. Business process reengineering
business process reengineering (BPR) is a strategy used for redesigning workflows from scratch. The first step in BPR is a complete analysis of existing workflows and a review of customer input. Managers who will implement BPR will create entirely new workflows that achieve organizational goals more efficiently.
4. Lean strategies
lean management methodology is a universal management tool for delivering value and optimizing workflows. Lean management is a business approach for maximizing customer value while minimizing waste. This methodology was first introduced by the Toyota Production System (TPS) to create a culture of continuous process improvement in an organization.
The main goal of lean workflows is to improve efficiency and effectiveness by reducing the time spent on non-value-added activities. Wasteful, inefficient practices like unnecessary meetings, tasks, and documentation processes, can be decreased with proper implementation of Lean strategies.
5. Six Sigma
this management method helps identify and remove the root causes of process deficiencies. Six Sigma methodology focuses on improving the capability of business processes by reducing the likelihood of error. This is a data-driven approach that uses a statistical methodology for eliminating defects and improving profits.
Trained Six Sigma experts use empirical and statistical quality management methods to determine the Sigma rating of a process. The rating determines the likelihood of the process producing a defect.
6. Theory of Constraints
Theory of Constraints (TOC) is a workflow optimization method that is useful in identifying and addressing the factors that limit or prevent an organization from achieving its goals. This optimization methodology takes a scientific approach to improvement by identifying the most important limiting factor that stands in the way of achieving a goal and systematically improving that constraint until it is no longer a limiting factor.
7. Total Quality Management
Total quality management (TQM) is the continual process of detecting and reducing or eliminating errors in manufacturing, streamlining supply chain management, and improving customer experience. TQM focuses on refining processes continually to eliminate inefficiencies and errors. TQM originated in the manufacturing space. This is a flexible tool that can be customized according to the unique needs of the team or organization.
Benefits of Workflow Optimization
There are several benefits of optimizing workflows. The most obvious benefits of optimizing a workflow are improved customer relationships, data-driven decision-making, and deeper visibility into a team’s progress. An optimal workflow can also reduce human error and make it easier to know when to scale up a business without hampering business outcomes.
Specific workflow optimization benefits include
1. Improved customer relationships
customers appreciate consistent and timely responses to inquiries and concerns. Streamlining workflows by implementing workflow optimization techniques helps eliminate workflow issues and frees up time to improve customer satisfaction.
2. Reduced bottlenecks
a process bottleneck is a congestion point in the workflow that delays process execution. Bottlenecks slow down production time, waste time, effort, and resources, and also impact profitability. Optimizing a workflow helps eliminate process bottlenecks.
3. Decreased waste
Wasteful activities are those that can be eliminated from the workflow without affecting the productivity of the process. Workflow optimization helps identify the wastes in the process and eliminates wasteful steps/tasks from the process.
4. Improved productivity
When the processing bottleneck is eliminated from the workflow, team members can complete tasks more efficiently and quickly. For manufacturers, higher levels of productivity can be achieved by optimizing manufacturing workflows.
5. Greater agility
Clunky and redundant workflows make it difficult for organizations to adapt to change or business growth. Workflow optimization streamlines workflows to remove cumbersome and redundant steps to empower the organization to adapt to growth opportunities and challenges.
6. Improved consistency
Optimized workflows provide clarity and enable all employees to adhere to a consistent standard of efficiency and quality.
7. Multitasking capabilities
As the organization grows, processes increase in number and complexity. Workflow optimization helps multiple workflows operate simultaneously without any resource contention. When managers streamline processes by using suitable optimization techniques, managing and controlling workflows becomes easier and more effective.
8. Enhanced work culture and team collaboration
Well-documented and streamlined processes make life easy for the employees because they spend less time firefighting and more time on activities that add value to the organization and their careers. With all the non-essential and labor-intensive tasks being taken care of by the automated workflow, employees can spend more time managing and completing successful projects.
Workflow optimization breaks down process silos and builds a more collaborative workspace where resources communicate seamlessly with one another. A more collaborative and positive work environment can be created by optimizing workflows.
Also Read: examples of how to improve work performance
9. Better compliance
Optimizing workflows brings about standardization in an otherwise chaotic and disorganized process. Standardized processes help organizations have better control over internal policies and regulations. When internal processes adhere to policies, they automatically comply with government-mandated compliance regulations as well.
Workflow Optimization Techniques
Managers can choose to optimize their workflows by following any of the optimization strategies mentioned above. The choice is mainly based on the nature and scale of business operations. The intent of optimizing workflows is the continuous improvement of processes by identifying and eliminating wasteful tasks. Workflow optimization techniques can help managers identify process issues, document them, and map new workflows that encourage consistency across the team and foster clear and objective decision-making.
How to Go About Workflow Optimization
A key step in optimizing workflows is identifying what is working in a process and what isn’t. A documented process provides all the information you need to determine which components need improvement and which need to go. Here are the steps that lead to successful workflow optimization.
- Preparatory steps for optimization – 4 crucial steps help you prepare to optimize workflows. The first step is reviewing the goals of optimization. Why are you considering changing or refining your workflows? Having a clear idea about the end goals and prioritizing the most essential components of the workflow is a must while preparing for workflow optimization.
- Review your current workflow – conducting a thorough review of existing workflows is essential for workflow optimization. The review must consider the parts of the workflows that produce the most errors or inefficiencies. To know more about current processes, we must interview team members who are most familiar with the way the process works. At the end of the review, all the steps must be organized into a comprehensive and chronological list.
- Determining constraints – in the majority of cases, processes do not perform at optimal levels. There are inherent limitations within the process that hold it back. Consult team members and review processes to determine the most common limitations in the current process.
- Identify bottlenecks – delays and bottlenecks are common in a process. Identifying and clearing bottlenecks is the main focus of process optimization. Where is the congestion in the workflow? Once process bottlenecks have been identified, you can strategize with managers and team members to ease the congestion and eliminate resource wastage.
The next most important part of workflow optimization is the documentation of workflows. Proper documentation of workflows improves visibility for the entire team. Accurate documentation will make it easy to identify areas of improvement. Lack of documentation and formal workflows tends towards the creation of silos, which bring down process efficiency. How to document a workflow? The following points are crucial considerations while documenting a workflow.
1. Focus on the ultimate goal
every task in the workflow should have a clear goal that must be aligned with the overall organizational goal. While documenting the workflow, every task must be linked to a clear goal.
2. Understand the scope of the process
some workflows may be confined to a single team, while others may be cross-functional or even implemented company-wide. Identifying all the team members or resources that are relevant to the specific workflow is part of identifying the scope of the process.
3. List the workflow steps
the best way to understand a process is by interviewing team members who are familiar with the process. All the workflow steps must be compiled into a single, comprehensive list.
4. Audit your workflow
it is not enough to understand the scope of the process or list out workflow steps, you need to audit the workflow to determine its relevance. Each step of the process must be reviewed, the relevance of each step must be determined, and the overall process must be refined for maximum efficiency.
5. Map your workflow
creating workflow maps or flow diagrams is an integral part of process documentation. Workflow maps are helpful visual tools that clarify what is working, and what isn’t in a given process. Directional arrows that indicate the direction of task flow must be included in the process map.
6. Analyze the workflow
workflow analysis is the next important step in process documentation. Once you have the process map, it becomes easy to analyze the workflow at a task level. Workflow analysis is the process of breaking down workflow performance and identifying trends. By studying workflow at the task level, the execution techniques can be streamlined for better outcomes.
7. Consider process variables
workflows must be customized based on inputs from team members and stakeholders. Even the time frames for each task must be estimated clearly. Even the time taken for review and decision-making must be included while calculating the time for each task.
8. Define roles and responsibilities
the roles and responsibilities of each team member in the process must be clearly defined. The names of team members responsible for each task in the workflow must be clearly defined.
9. Refine and finalize
once the documentation is complete, the next and final step is to review it with the team members. The document should be reviewed with the team and necessary approvals should be acquired before implementing the new documenting process.
Understanding and optimizing workflows is an integral part of managerial responsibilities. Organizations must take workflow optimization seriously and include it in the planning of business operations.
Workflow Optimization Examples
For businesses to adopt suitable workflow optimization techniques, an overview of successful workflow optimization examples is necessary. When you see how workflow optimization has worked for real organizations, you are convinced to adopt optimization techniques suitable for your business.
Automating work orders
One of the world’s busiest airports used Excel documents to schedule work orders in the facilities management function. This was done manually, which was time-consuming and prevented real-time reporting. Work order processing was optimized by automating the workflow, which reduced the processing time to 20 minutes from 30 hours per week.
Procurement automation
The procurement and payment process is among the most labor-intensive and tedious processes in a business. In a large enterprise, the procurement process took up to 100 days to complete payments via manual processing. When an automated procurement platform was created for tracking purchases, payments, and vendors, over 160 hours of wasted time were saved for the company.
Using Software to Optimize Workflows
Automation using workflow automation software like Cflow improves work methods and streamlines key business processes. Workflow automation or workflow optimization software helps generate business-critical documents, assign tasks, digitally sign documents, and send, and store data across multiple systems.
Cflow is a cloud BPM software that can be customized according to the requirements of your business. From procurement to finance to accounting – all the key business functions can be optimized using our workflow automation software. To gain a competitive edge in a digitally powered market landscape, workflow automation is a must. Applying these workflow optimization techniques reduces the need for manual, wasteful effort. Interested in exploring Cflow further? Sign up for the free trial to experience effective workflow optimization.