Differentiate your Business through Continuous Process Improvement
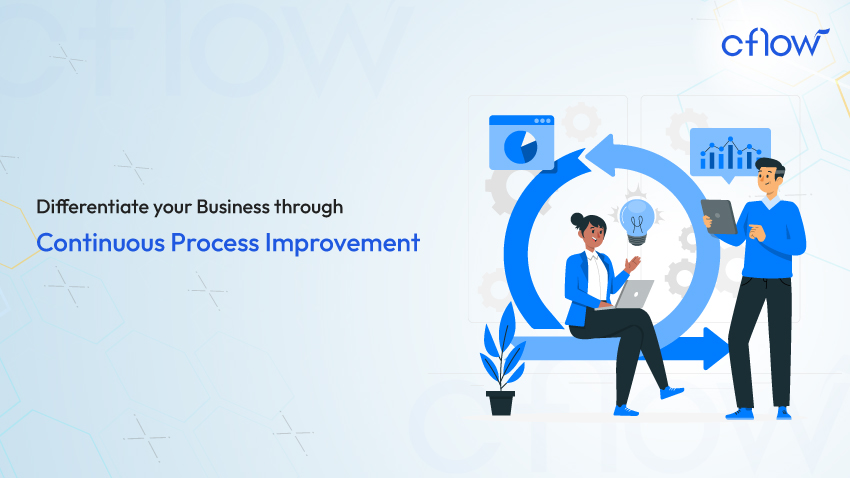
Key takeaways
- Continuous process improvement (CPI) is a methodology that focuses on continuous improvements to products, services, or processes.
- Continuous improvement is done by examining and improving business processes to eliminate bottlenecks by using the best software option and management methodology.
- CPI improves productivity, efficiency, customer experience, workforce engagement, agility, resilience, competitive edge,
- Cflow is your process automation partner for sustained business process improvement and innovation.
What is a Continuous Process Improvement (CPI)?
To survive in a dynamic market and ensure long-term business gains, businesses need to evaluate and improve their processes continuously. Continuous process improvement (CPI) is a methodology that focuses on continuous improvements to products, services, or processes. Changes or improvements can be done gradually or in one go. The important aspect of CPI is that it is an ongoing activity rather than a one-time initiative.
Table of Contents
Continuous Process Improvement Model
The most commonly used continuous improvement model is the Plan-Do-Check-Act (PDCA) cycle. There are countless ways to build a culture focused on process improvement. Finding the right strategy to use for the unique industry can be difficult. Process improvement efforts must be focused on performance, commitment, strategy, and workflow.
The entire process of continuous improvement can be based on the following steps in this model –
Plan
Identify an opportunity for improvement and plan the change. Not all processes are suitable for continuous improvement, so it is important to identify an opportunity that is suitable for continuous improvement. The improvement plan must be catered according to the process.
Do
The best way is to implement a change in phases or on a small scale. This way it is easy to control the implementation and evaluate the results.
Check
Post implementation, the performance data needs to be gathered and analyzed. The data needs to be analyzed to evaluate the results of the change. Data after the changes are compared with the previous performance data to determine if it has made any difference.
Act
Analyzing the data will reveal whether the change was successful or not. If the change is successful, then implementation can be carried out on a larger scale. Large-scale implementation also must be followed up and results must be assessed continuously. If the change does not work, then the PDCA cycle must be restarted.
Differentiate your Business through Continuous Process Improvement (CPI)
Markets are changing rapidly. Consumer requirements are changing rapidly. The need for product/service innovation is increasing rapidly.
Is your business improving and evolving continuously in tune with these changes?
Is continuous process improvement at the core of your business strategy?
Organizations that focus on continuous improvement become increasingly competitive and can maintain an edge over competitors. Continuous improvement of businesses ensures that processes, methods, and practices are accurate, effective, and efficient.
Continuous improvement is done by examining and improving business processes to eliminate bottlenecks by using the best software option and management methodology. CPI on the other hand focuses only on processes to evaluate if they are meeting the company goals. Making incremental changes that provide long-term business benefits is the main aim of CPI.
Need for Continuous Improvement
Continuous improvement processes are more than just improving efficiencies. Successful and complete implementation of continuous improvement cultivates a culture of innovation and ownership that provides a competitive advantage and drives ongoing growth and success. Implementing continuous improvement provides several benefits for the business. The need for continuous improvement in any business is reiterated by the benefits it brings to the business
Improves productivity and efficiency
Continuous improvement efforts optimize processes, which enables organizations to do more with less. The operating costs are also significantly reduced, which in turn increases productivity.
Superior customer experience
Continuous improvement efforts are instrumental in improving the quality of products and services. When better quality products and services are delivered, customer experience is improved significantly. Businesses that are committed to continuous improvement, are capable of delighting customers with constant updates rather than doing damage control.
Promotes a more engaged and empowered workforce
continuous improvement provides opportunities for continuous learning and growth for teams and individuals. An aligned workforce is more effective in identifying areas for ongoing improvement, which leads to the development of new skills and knowledge. A skilled and talented workforce in turn improves employee experience and work satisfaction.
Builds agility and resilience
An organizational culture that is committed to continuous improvement translates to flexibility that is built into every grain of the operational strategy. Such a culture makes it easier to respond to evolving customer needs and enables the organization to stay compliant with regulations and adapt easily to market needs.
Builds competitive edge
Continuous improvement efforts across teams help focus on improving process results, which in turn leads to more innovative products and services. Continuous improvement of processes helps businesses gain a competitive edge and establish themselves as the market leader.
Also Read: 7 Simple Ways to Improve at Work Today!
Continuous process improvement tools are as below:
Business process mapping
Creating a business process map helps you understand every process better. A simple flowchart mapping the entire business process helps in understanding the process loopholes, redundancies, and areas of improvement.
Deming Cycle
Once the process flowchart is created, Deming’s cycle can be implemented for process improvement. The Deming Cycle, also known as PDCA, is a 4 step process improvement technique. The 4 steps are to plan, do, check, and act.
Process management software
Digital processes and software can be created to ensure that business process improvements work successfully. A business process management system (BPMS) routes tasks between employees, which ensures that the task is completed efficiently.
Continuous Process Improvement (CPI) Strategies
When done right, continuous process improvement enables businesses to realize long-term cost benefits and gain a competitive edge. Some methodologies or strategies can be categorized as continuous process improvement techniques.
Choosing the right methodology as per your business requirements holds the key to successful CPI implementation.
Some of the improvement methodologies are:
Value Stream Mapping
This methodology is compatible with all other business process improvement strategies. A company’s design and flow of processes are evaluated from the perspective of value addition. A properly planned value stream will contain all the details of business processes. This helps identify those areas in the continuous improvement process that add value and those that do not add any value. Elimination of the latter steps from the process helps optimize the process.
Lean and Continuous Improvement
This strategy aims at eliminating waste throughout the company. Anything that doesn’t add value to the business is considered waste.
Kaizen
This is a popular improvement strategy that has been around since the 1980s. The primary aim of the Kaizen method is to focus on improvements in many small business areas rather than a few larger changes. Capital investments, an engaged workplace, and long-term improvement are some of the benefits of implementing the Kaizen method.
The 5S Strategy
This strategy focuses on organizing a workplace for improving efficiency and effectiveness. Each step in a continuous improvement process is evaluated to identify the needs of the step and ensure the availability of the requirements.
Total Quality Management
This strategy was originally used in the manufacturing sector. The focus of TQM is on improving employee involvement, customer satisfaction, customer engagement, and other elements within the organization. This strategy can be used alongside other strategies.
Plan-Do-Check-Act (PDCA)
This is the most commonly followed continuous improvement methodology that spans 4 steps to identify, test, and implement changes that focus on improving a process. This is a scientific method that focuses on measuring and analyzing results to identify the actions needed for improvement efforts. This method was developed in the 1950s by a statistician and engineer.
Six Sigma
This is a popular method that was originally designed to improve the quality of processes by eliminating defects and minimizing process variability, with the help of data and statistics. The main focus of the Six Sigma model was on the customer, eliminating issues or defects, flexibility, collaboration, and continuous improvement. There are 2 main sub-methodologies in Six Sigma – DMAIC (Define, Measure, Analyze, Improve, Control) and DMADV (Define, Measure, Analyze, Design, Verify).
Theory of Constraints (TOC)
This methodology focuses on identifying the biggest bottleneck in the process, or the major constraint in the process. This concept hinges on the idea that identifying and addressing the biggest system constraint is the most effective path to improvement and continuous growth. The chain analogy is followed in this approach to underscore the importance of identifying a system constraint. Identify, exploit, subordinate, elevate, and repeat are the steps followed by the TOC approach.
End-to-end workflow automation
Build fully-customizable, no code process workflows in a jiffy.
Business Process Management and CPI
Business process management techniques are used for CPI. Continuous process improvement is a set of methodologies that are used to improve business processes for long-term cost and performance improvements. BPM is implemented for specific business processes to remove redundancies and repetition.
CPI focuses on improving processes, products, and services continuously by adopting various improvement methodologies. BPM software is designed based on process workflows for optimizing the continuous improvement process flow. CPI is usually an umbrella of improvement software that aims at long-term business benefits.
A no-code cloud BPM software like Cflow enables businesses to improve and optimize their business processes within minutes. Cflow comes with an easy-to-use visual form builder that lets you set up workflows within minutes. Finance, procurement, marketing, and HR workflows can be easily set up using Cflow.
Implementing Continuous Improvement
Several strategies and methodologies help organizations implement continuous improvement. In a majority of cases, companies do not follow a single improvement strategy, but combine 2 or more strategies or merge new methodologies with existing technologies to meet their specific needs. Regardless of the methodology chosen to implement continuous improvement, successful implementation must follow the steps listed below –
Definition of scope
Identify a process that requires improvement and proceed to establish goals and objectives for the improvement of the process. Successful continuous improvement efforts are those that focus on making ongoing, iterative changes to the process.
Building a team
Who will be leading and supervising the continuous improvement efforts? Who will be the team members implementing the change? All these points should be clarified while building the team for driving the continuous improvement initiatives.
Identifying improvement opportunities
A thorough understanding of the way current processes are executed and the areas of wastage, inefficiency, and improvement need to be identified.
Developing an improvement plan
Once areas of improvement have been identified, the next step is to create a plan for making changes. The plan must define priorities clearly, identify measurable goals, and establish a project timeline.
Implementing the plan
The best approach is to implement the plan on a small scale first and then expand the scope based on the success rate.
Monitoring the progress
Monitoring and measuring the success of the implementation is crucial to verify if the efforts are on track. Tracking the progress and comparing it with previous performance data helps teams understand if they are headed in the right direction.
Continuously improve
Reviewing the the process continually and documenting the learnings from failure and setbacks, is an important aspect of continuous improvement initiatives.
Conclusion
Continuous process improvement helps businesses survive sustain market competition and deliver innovative product and service ideas. Choose a CPI methodology that brings out the best in your business. Continuous process and product improvement are key to business differentiation.
Cflow is your process automation partner for sustained business process improvement and innovation. All you need to do is sign up for a free trial of Cflow to unleash the powerful capabilities of your business processes.
What should you do next?
Thanks for reading till the end. Here are 3 ways we can help you automate your business:

Do better workflow automation with Cflow
Create workflows with multiple steps, parallel reviewals. auto approvals, public forms, etc. to save time and cost.

Talk to a workflow expert
Get a 30-min. free consultation with our Workflow expert to optimize your daily tasks.

Get smarter with our workflow resources
Explore our workflow automation blogs, ebooks, and other resources to master workflow automation.