Process Improvement Tools to Optimize Business Performance
May 8, 2025
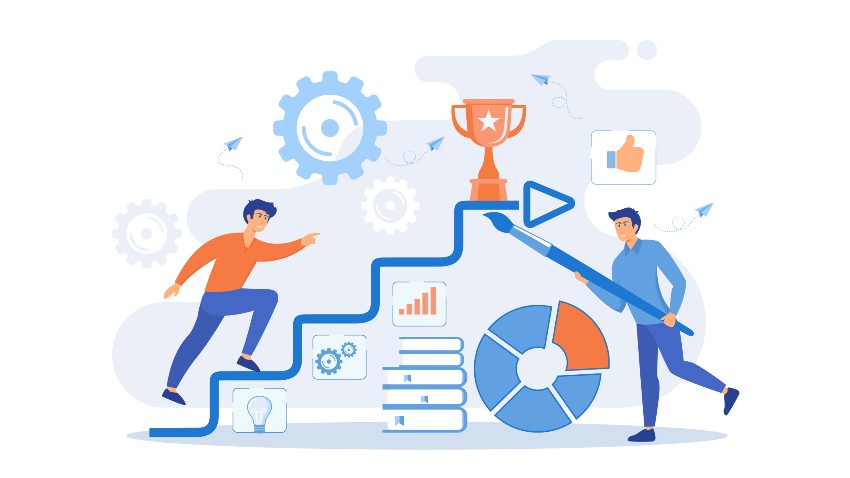
Key takeaways
- Process improvement tools provide organizations with systematic methods to understand processes better and implement process improvement techniques.
- Process improvement or optimization is a form of quality management that proactively identifies inefficiencies so that improvement steps can be taken immediately.
- The main goal of lean process improvement is to enable customers to find ways to deliver more value to their customers.
- The different types of process improvement tools include process mapping software, process analysis tools, improvement frameworks, process automation tools, etc.
- Cflow is a no-code BPM automation solution that simplifies process improvement.
Table of Contents
Key Concepts of Process Improvement
Businesses that are in a constant state of change and improvement are more successful in overcoming market challenges and aligning to changing customer requirements. Process improvement may seem straightforward in theory, but is a challenge for practical implementation. Process improvement is the task of identifying opportunities for improvement, implementing changes, and measuring the impact of these changes. Process improvement requires a structured and continuous approach to changing and improving business processes and operations. Kaizen or Continuous improvement is a Lean process methodology that provides a disciplined approach to business process improvement. The key concepts in Lean process improvement include:Process improvement is a mindset, not a single event
Lean process improvement is a methodology that considers improvement as an ongoing practice and a mindset, rather than an event. Lean organizations consider continuous improvement as a daily mindset and practice that enables organizations to deliver on their promises to customers. This approach is more successful when it is practiced across the organization, rather than departments or teams. Lean improvement helps you maximize value and deliver faster results The main goal of lean process improvement is to enable customers to find ways to deliver more value to their customers. This is achieved through a systematic and scientific approach to practicing continuous improvement as part of daily tasks. Planning, executing, reviewing, and identifying – are the steps in the continuous improvement cycle. Also Read: 3 ways to improve work performance
The two main techniques in process improvement are Kanban and WIP limits.
Kanban is a visual process workflow tool that enables individuals, teams, or organizations to manage work through a shared understanding of the process. This technique enables teams to identify opportunities for process improvement Kanban boards are used for managing work by automatically generating data that can be used to evaluate the impact of continuous improvement efforts.
Implementing the work-in-progress (WIP) limits for individuals and teams is another important Lean process improvement technique. The limits in WIP methodology are fixed constraints that teams place on themselves to improve throughput and minimize context switching.
The WIP limits help teams deliver higher-quality work faster. WIP limits can be easily tracked using Kanban boards by counting the number of cards in the “in-process” lanes of the workflow. WIP limits can be set for specific lanes in the Kanban boards which when exceeded issue alerts to the concerned authority. Manual override of the WIP limits can also be done for specific exceptions decided by the team.
Various process improvement tools and techniques are designed based on lean continual process improvement methods. A process improvement tool can be used to implement the key concepts of lean process improvement.
Why is Process Improvement Important?
A majority of organizations are taking process improvement seriously and adopting several people process tools to upgrade their business processes. But, why is process improvement needed in the first place? Continuous improvement is the key to streamlined and optimized business operations. Redundancies and inefficiencies within business processes may lead to bottlenecks that result in indefinite delays, excess costs, inaccuracies, and poor output quality. Process improvement or optimization is a form of quality management that proactively identifies inefficiencies so that improvement steps can be taken immediately. Identifying the root cause of process inefficiencies indirectly pinpoints ways to improve each current process. Irrespective of the method you choose for improving the process, the result is:- Increase in process speed
- Increase in accuracy
- Reduction in costs
- Improved transparency
- Quality end products
- Better customer and vendor relationships
- Improved productivity
- Improved customer satisfaction
What are Process Improvement Tools?
Process improvement tools provide organizations with systematic methods to understand processes better and implement process improvement techniques. The 3 main categories of process improvement tools are:- Process mapping tools
- Problem-solving tools
- Process improvement tools
Here is Why Process Improvement is Important for a Business:
Improved customer satisfaction – By implementing process improvements, the quality of end products/services is improved considerably. This automatically improves customer satisfaction. An improved process is completed in less time than a non-optimized process, which also contributes to customer satisfaction. Time and money saving – Process improvements essentially result in the elimination of redundant steps and automation of repetitive, low-value tasks. As a result, the time taken to complete a process and the associated costs are reduced. Strengthens customer retention– Streamlined processes result in better customer engagement. Customers that are actively engaged are bound to stay loyal to your organization. Boost project success rate – Implementing process improvement techniques helps manage business processes more effectively. Efficient management of processes results in higher project success rates. Improve business agility – Keeping up with the increasing pace of business operations requires improvements to the processes. Processes need to be agile and flexible to keep up with growing market demands. The right process improvement steps help improve the agility and flexibility of business processes. Gain a competitive edge – If an organization is not continuously improving, it likely falls behind the competition. It is important to regularly review existing business processes and make appropriate improvements to enhance process performance. Improve operational efficiency – Streamlined processes help maintain order and consistency of business operations. Continuous improvement of business processes eliminates redundancies and bottlenecks, which in turn improves operational efficiency. Process improvement may involve a sequence of actions, such as improving processes, reducing costs, or elevating profits to achieve new objectives and goals. These actions may comprise particular techniques or methodologies to increase the odds of achieving successful results.9 Steps to Process Improvement
Poorly implemented process improvement results in higher costs, fragile infrastructure, and frustrated teams Implementing process improvement initiatives requires careful planning. Here are 9 steps to successful process improvement implementation –1. Map out the current process
The first point to consider once you decide to improve your business processes is “How do we do things now?”. Mapping out current processes via visual diagrams or maps is the best way to understand the process flow and identify the cause of delays and bottlenecks. Compared to text-based process management methods, visual process maps or flow diagrams are extremely important to identify areas that need improvement. Clearly defined process improvement steps help identify some of the most common sources of inefficiencies that can be eliminated. Visual maps must include all the steps in the process, the time taken to complete each step, and outline who works on each step.2. Define business goals
What are your big-picture goals? What are the business challenges that need to be addressed via process improvements? Once a business decides to practice continuous improvement, it pays to find clear answers to questions like the ones mentioned here. The best place to start is to determine organizational goals. Establishing clear objectives and key results or OKRs helps create measurable business goals. The next step is to consider team and personal goals.3. Analyze what needs to be changed
Almost all business processes have some amount of redundant steps within them that do not add value to the customer. Identifying these steps will help save time and produce higher-quality results. Some of the types of wasteful steps include overproduction, non-utilized talent, undue delays, inefficient movement of people, and sitting inventory.4. Redesign processes
Once the process maps are in place, business challenges have been identified, and required changes are analyzed – the next step is to start finding solutions for the challenges. Each of the pain points or challenges identified in the previous steps requires solutions. Rather than going for the first obvious solution, a deeper investigation into the solution is required. The proposed change (solution) must not only the process in consideration but associated processes as well.5. Implement the changes
Once the changes are finalized, the next step is to implement them. It is better to take a measured approach during implementation so that the impact of the changes can be measured. Implementation carried out in stages or phases is better than complete implementation.6. Creating open streams of communication
Establishing clear paths of communication and collaboration is important for the successful implementation of process improvements. Clear communication paths eliminate boundaries and facilitate the participation of team members.7. Identifying process KPIs
The impact of process improvement initiatives must be measured to determine the success of implementation. Clear KPIs must be established to measure the progress of new changes. A streamlined system to gather metrics must be set up to measure how process improvement steps help reach goals. The data gathered for analyzing metrics must be clean and authentic.8. Continuously monitor process improvement efforts
Employees, teams and the leadership must continuously monitor process improvement efforts to ensure that they are on track. There are specific tools for process improvement that can be used for monitoring the performance of process improvements.9. Measure the impact of process improvement efforts
Designing ways to measure the impact of process improvement initiatives is important. To know if the process improvement was working, you need to conduct regular meetings to review performance activity and regularly discuss the performance of current or recently completed improvement projects. The right process tools help you measure the impact of changes.
Also Read: 3 ways to improve at work performance
Types of Process Improvement Tools
Process optimization tools provide businesses with a systematic approach to improving business processes. Depending on the purpose of the process tool, it is classified into 4 types.1. Process Mapping Software
Mapping out business processes is the first step to improvement. Process mapping software is used for creating a visual representation of the process to plan out the flow of the new or current process. Mapping out a process gives you a better idea of where the process requires improvement, as well as the causes of process bottlenecks. The two popular types of mapping tools include.- SIPOC Diagram: SIPOC stands for Suppliers, Inputs, Processes, Outputs, and Customers. These diagrams are used to break the process down into what goes in, what happens, and what comes in and out. The supplier in this case would be any stakeholder that provides input to the process. The input is anything that goes into the process, such as materials, time, staffing, and equipment. The process outlines each step in the process sequentially. The output column lists the results. Finally, the customer is the person who receives the outputs. The SIPOC technique is suitable for straightforward processes that do not include conditions.
- BPMN Process Flowcharts: This is a unified modelling language that is understood and accepted by people to model business processes. BPMN uses a well-known set of symbols to map out the business activities within a process. This diagram shows possible conditions for processes with multiple potential outcomes based on different decisions. The technique is best suited for processes that follow different conditional paths.
2. Process analysis tools
These tools enable stakeholders to get to the root cause of process bottlenecks. Process analysis tools help in problem-solving, and breaking down the process into tasks so that problems can be identified easily. These roles help you get to the root cause of process inefficiencies.- Fishbone Diagram – This is a type of cause-and-effect diagram that looks at a particular problem and works backward to get to the root cause. The problem is at the mouth of the fish, and the solution is towards the other end.
- Whys Analysis – The 5 Whys analysis is a root cause analysis that digs deep into the problem. You just ask the “why” five times in this process to get deep into the root cause. For example, if the issue is about late or delayed payment from a customer, the 5 whys would be why are they refusing to pay; why hasn’t anyone taken responsibility; why were spares not ordered; why was the order not delivered on time; and why did we run out of stock.
3. Improvement Frameworks
Improvement frameworks form the basis for process improvement. The techniques within the improvement frameworks serve as an improvement tool that can help compare possible solutions to see how they measure up to the performance of the current process. The 3 commonly used process improvement tools are:- DMAIC – Stands for Define, Measure, Analyze, Improve, and Control. This technique is adopted from the Six Sigma methodology. This process improvement method helps define the problem that needs to be solved; measure the performance of the current process; analyze the process and identify potential improvements; put solutions into practice; and track the performance of improvements.
- PDCA – Stands for Plan, Do, Check, and Act. This lean methodology tool provides a technique for testing improvements before implementing them at scale. Plan: plan the change based on your analysis of the problem. Do: implement the change into the current process. Check and monitor the performance of the improvement. Act: take action to scale the improvement method or create a new solution if the current solution is not working.
- DRIVE – This technology is similar to the DMAIC technique. DRIVE stands for Define, Review, Identify, Verify, and Execute. Define the scope of the problem with the help of measurable criteria. Review the current process. Identify likely solutions. Verify that improvements would bring the desired results. Execute the implementation.
4. Process Automation Tools
These tools provide active process improvement solutions for various business processes. BPM tools like Cflow cut out ineffective manual processing by automating workflows.End-to-end workflow automation
Build fully-customizable, no code process workflows in a jiffy.
Features of Process Improvement Tools
Choosing the process improvement tool for your business requires scrutiny of the features provided by the tool and comparing them against your business requirements. Some essential features process automation tools must have- Visual workflow builder – Creating workflow forms must be an easy and quick affair with the automation tool. Visual drag-and-drop form builders simplify the process of creating process workflows. Document management – Process data needs to be managed safely and securely. Data encryption of crucial process data is a must in automation software. Integration – Business systems are typically interdependent. Seamless integration of business automation software with other systems is a must-have feature. Reports and analytics – The automation software must provide real-time reports and analytics on the status of processes. Complete information on process cycle times, bottlenecks, and inefficiencies can be derived from these reports. Pricing – The software must provide complete value for the money. The pricing of the software must be cost-effective in terms of the features it provides. Most automation solutions provide several features, some of which may not be relevant to your business. So you need to choose the solution that provides features that are needed for your business. If you are looking for process automation solutions for streamlining your business processes, then Cflow caters to all your business requirements. Cflow provides a host of features that streamline process workflows quickly and effectively. The visual workflow form builder allows users to create customized forms as per the unique requirements of the business. Cflow provides a unique “public forms” feature that allows users to create forms that reach a larger audience. With Cflow, you can seamlessly integrate with over 1000 third-party applications when you require more features or external support besides what Cflow already offers. Data encryption and security features in Cflow offer the highest level of reliability and protection for your data. Following up on approval-based workflows is super easy with Cflow via email notifications and alerts. The best part is you can approve or reject by replying to the email without even logging into the application.Conclusion
Improving the sustainability of your business operations is not a stand-alone event, but a continuous process. Business process improvement tools play an important part in the continuous improvement initiatives that businesses undertake. From Kanban to Six Sigma to Lean management methodologies – there are several process improvement techniques that businesses can adopt. Process improvement tools not only help improve processes, but they help in mapping and analyzing the process as well. Choose process improvement tools and techniques that work well for your business requirements. Cflow is a no-code BPM automation solution that simplifies process improvement. To explore our feature-rich workflow automation software, sign up for the free trial right away.What should you do next?
Thanks for reading till the end. Here are 3 ways we can help you automate your business:

Do better workflow automation with Cflow
Create workflows with multiple steps, parallel reviewals. auto approvals, public forms, etc. to save time and cost.

Talk to a workflow expert
Get a 30-min. free consultation with our Workflow expert to optimize your daily tasks.

Get smarter with our workflow resources
Explore our workflow automation blogs, ebooks, and other resources to master workflow automation.