10 Reasons Why Lean Process Improvement is a Must for your Business
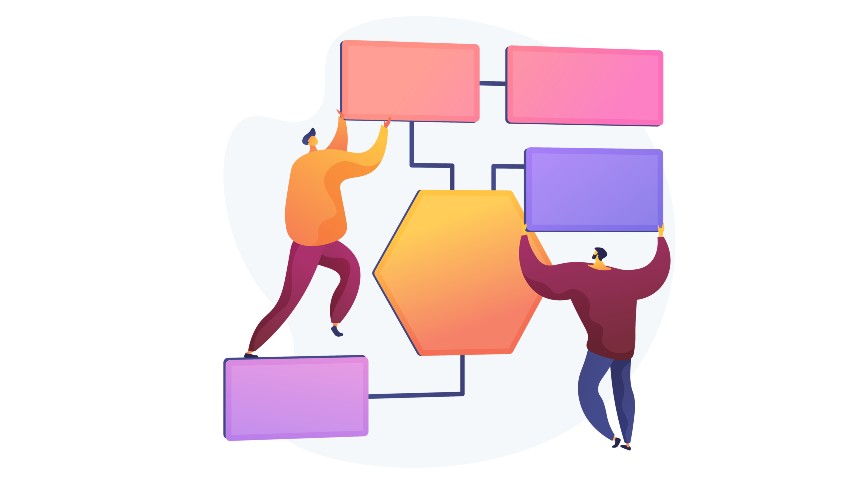
Business efficiency is directly proportional to the efficiency of its processes. Efficient business operations require process improvement.
Why You Need a Process Improvement Methodology
Streamlined process workflows cut our process redundancies to improve productivity and operational efficiency. Broken business processes can cost you time and money. Process standardization, process streamlining, process automation, and outsourcing are some of the ways to improve work processes and efficiency.
What is Process Improvement?
Business process improvement (BPI) is the proactive task of identifying, analyzing, and implementing new business workflows to optimize company operations and deliver exceptional customer service. Businesses looking to stay competitive in dynamic market scenarios and improve employee and customer engagement adopt process improvement methodologies.
The definition of process improvement is the ongoing practice of optimizing existing business processes to meet the best market standards and improve customer engagement. The different methodologies in the process improvement family are Lean, Six Sigma, Lean Six Sigma, Rapid Improvement, Total Quality Management, and Theory of Constraints.
Lean process improvement techniques were born out of manufacturing practices. These principles encourage continuous process improvements that are focused on people. What is a lean process? Businesses that do not follow a structured and continuous approach to process improvement are bound to lose growth momentum. Lean continuous process improvement methodology is based on 5 principles that focus on improving workplace efficiency.
Also Read: 3 top ways to improve work performance
The 5 Principles of Lean Process Improvement Methodology Are
1. Defining value:
Defining customer value is the first principle of lean process improvement. Value is what the customer is willing to pay for. To deliver full value to the customer businesses need to discover the actual and hidden customer needs. Gathering information on consumer demands and behaviour is done through surveys, interviews, web analytics, and demographic information. Qualitative and quantitative analyses are adopted to understand customer requirements, mode of delivery, and product price expected.
2. Mapping the value stream:
Identification and mapping of the value stream is the second lean principle. Once customer value has been identified, all the business activities that contribute to these values are identified. The processes that do not add value are considered waste. By reducing and eliminating these redundant processes, businesses can deliver complete customer value and also reduce production and operational costs.
3. Creating a smooth flow:
Once redundant steps have been removed from the process, the remaining steps are organized for smooth process flow. An organized process flow can be established by breaking down the process into steps, reconfiguring the production steps, reassigning the workload to appropriate resources, and creating cross-functional tasks.
4. Establish pull:
Ensuring that just the right number of resources are utilized for manufacture and that they are available at the time needed is the basis of the pull-based system. Pull-based systems are always created to meet the needs of end-users.
5. Pursue perfection:
Following the above steps ensures that wasteful steps in the processes are cut out. Essentially, lean process improvement steps must be made part of the organizational structure. Every employee must be aware of lean quality improvement steps and follow them in their work routines to achieve perfection.
Process improvement techniques outlined in the business process improvement methodology enable businesses to maintain a continuous improvement culture. Following lean process improvement steps creates smooth and efficient process workflows, which in turn improve business productivity and revenue.
The key components of lean improvement focus on increasing customer value, optimizing operations, and eliminating redundancies. Not only does lean process management reduce wastage and improve process efficiencies, but it also builds a culture that respects all employees.
Business process improvement focuses on:
- Reducing process completion
- Identifying redundant efforts
- Improving work quality
- Ensuring regulatory compliance
- Minimizing friction between processes
Fine-tuning business efforts and operations for the smooth running of businesses is the ultimate aim of process improvement techniques. Breaking down organizational processes and resources to uncover ways to improve process efficiency by freeing employees to focus on more strategic initiatives can be done through lean process improvement techniques.
What is a Continuous Improvement Model?
Continuous improvement is a process improvement framework that is more of a mindset rather than a siloed event. It is an active and intentional business practice that is followed across the entire organization.
Continuous improvement models give structure to the continuous improvement practice. Continuous improvement is the most important pillar upon which lean management is built upon. Six Sigma and Kaizen are two important continuous improvement models.
Six Sigma is a widely recognized version of the Lean work process in business. The main focus of Six Sigma is to improve predictability and eliminate variability in processes. The main goal of the Six Sigma model is to achieve stable and predictable process results by following clearly defined and measurable processes.
This model is a disciplined, data-driven approach to continuous process improvement methodology. The basis for this model is statistical analysis. This model is best suited for organizations already organized in a structured corporate way.
Kaizen is a Japanese term that means “changing for the better”. Kaizen principles aim at improving both flow and process. This continuous improvement model is less rigid and structured than the Six Sigma model. Flow Kaizen efforts are directed towards the flow of materials and information.
Process Kaizen efforts aim at continuous improvement of individual and team processes, in other words, process flow improvement. Methodical experimentation while making changes and measuring the results is characteristic of the Kaizen model.
The success of the lean continuous improvement process depends on how the organization adapts to changes. Rather than being viewed as a siloed lean event continuous process improvement must be practised across the organizations.
Techniques of Lean Process Improvement
There are several process improvement methodologies that help organizations improve operational efficiency. Each of these methods aims to identify process issues, fix them, and analyze the success or failure of the changes. Although all BPI methods have a common goal, they suit the different needs of organizations.
Some of the frameworks focus on lean core concepts, while others get the company culture in the right place for process improvement. Certain lean and continuous improvement principles are also used for visually mapping out process workflows. We have already discussed the Kaizen and Six Sigma models; the other business process improvement methods are discussed below.
5S Model:
This is part of the Kaizen and Lean methodologies. 5S stands for the steps in process improvement, such as sort, straighten, shine, standardize, and sustain. Following this method brings consistency and standardization into process improvement.
Plan-do-check-act (PDCA) methodology:
This methodology is also a Kaizen methodology which stands for plan, do, check, act. It is very effective in helping companies identify processes that require improvement. Identifying the problem (plan), creating and implementing a solution (do), evaluating effectiveness through data (check), documenting the results, and implementing the solution if successful (act) are the various steps in the PDCA methodology.
SIPOC analysis:
This is a visual analysis format under the Six Sigma method. SIPOC analysis is done during the measuring stage of DMAIC (Define Measure Analyze Improve Control) or DMADV (Design Measure Analyze Design Validate) process improvement methods. This method enables organizations to define and establish a process improvement project and identify elements and requirements before implementing a process improvement method.
Cause and Effect Analysis:
The cause-and-effect analysis is part of the Six Sigma methodology. This is a diagramming method used for identification of the problem, discovering process roadblocks, and identifying reasons why the process isn’t working.
Value stream mapping (VSM):
The visual representation of customers’ perceptions of a business is the main focus of value stream mapping. VSM helps identify the value addition of the product, service, or process to the organization. The main focus of this technique is to eliminate waste, and redundancy, and adopt a lean approach.
Total Quality Management (TQM):
This process improvement method is focused on building long-term business success by improving customer satisfaction. TQM ensures that the entire company is onboarded on continuous process improvement. It encourages a culture where employees are driven towards a shared business goal.
Process mapping:
This is a process workflow visualization that aids in mapping out business processes. Process flowcharts, process charts, process models, and functional flowcharts are other ways of referring to process mapping. This is a thorough visual representation of a process from start to finish.
Kanban:
Kanban is a process workflow visualization method that brings the leadership, business units, and employees on the same page. Kanban is a lean process improvement methodology.
Need for Process Improvement
Process management and improvement techniques aim at eliminating process bottlenecks in business operations. Adopting process improvement methodologies helps eliminate waste from any part of the company. Process improvement analysis aims at defining business value from a customer’s perspective and creating low-cost, efficient ways to achieve it. Service process improvement, product process improvement, office process improvement, or even information technology process improvement are various departments where business process improvement can be implemented.
10 Reasons Why Lean Improvement is a Must for Your Business:
- 1) Promotes business growth: As businesses grow, they need to manage more customers, more employees, and increasingly complex processes. Progressive businesses that have several processes running need process improvement techniques for better operational efficiency. Process improvement provides better control and standardization over business processes.
- 2) Launches new products and services: before introducing new products or services, a review of existing processes is required. Continuous improvement techniques can help in improving the quality of new products and services.
- 3) Regulatory Compliance: The successful running of the business requires compliance with government, industry, and safety regulations. Businesses spend a lot of effort and time reviewing and modifying processes to ensure compliance with ever-changing compliance standards. Process improvement tools help businesses ensure regulatory compliance.
- 4) New business ventures: startup businesses need to focus on selling their products/services. They would need a standardized process for maintaining quality and consistent customer service. Process improvement methodologies help standardize their processes to maintain the efficiency and consistency of processes.
- 5) Cost reduction: redundant and repetitive tasks lead to higher process costs. Process improvement techniques help streamline business processes by eliminating redundant processes, which in turn reduces process costs.
- 6) Upgrading processes: Manufacturing concerns need to upgrade their processes to keep up with the latest technological trends to gain a competitive edge. Process improvement techniques help in the easy and efficient adoption of technology into existing processes.
- 7) Employee onboarding: as businesses grow, they hire more employees. Handling increasing employee numbers requires a planned methodology for passing strategic priorities from leadership to employees. A process improvement method improves the delegation process and the effectiveness of the work execution.
- 8) Improve sales: analysis of sales processes is required to identify the impediments that are retarding your sales. A sales and marketing process improvement methodology helps identify the impediments and identify the solutions to overcome them.
- 9) Manage mergers and acquisitions: successful mergers and acquisitions require seamless alignment of different business processes and cultures. Turning to process improvement enables businesses to carry out mergers and acquisitions without any duplications or wasted effort.
- 10) Measurable outcomes: process improvement allows for effective measurement of process outcomes. That which can be measured can be improved. Tracking and monitoring processes become easy with process improvement techniques.
- The best way to implement process improvement is to drive it across the organization. Well-trained and informed employees can be process improvement ambassadors. Implementing process improvement techniques at the right time and the right way ensures sustained business success.
End-to-end workflow automation
Build fully-customizable, no code process workflows in a jiffy.
Benefits of Process Improvement
Running a sustainable business requires continuous process improvement. All business processes need to be updated and upgraded according to dynamic market and consumer trends. Relying on outdated processes brings down operational efficiency and productivity. Business process improvement helps identify the biggest growth opportunities and improve customer engagement. Here are the top benefits of Lean process improvement.
Productivity:
Businesses that follow labour-intensive processes run the risk of inefficient and retarded process outcomes. Employees are forced to spend time and effort on low-value admin tasks rather than strategic project work. Introducing process improvement techniques frees employees from mundane tasks to focus on important project-related work. Reducing human intervention in business processes improves speed, accuracy, consistency, and productivity.
Employee engagement:
Process improvement tools automate repetitive tasks so that employees are freed from performing these tasks. Well-planned and defined business processes motivate and engage employees to contribute actively towards overall organizational goals. Smoother processes lead to a happier and more satisfied workforce.
Risk management:
Manual transformation of information between systems increases the risk of fraud and mistakes. Locating and fixing mistakes in manual processes takes a longer time. BPI tools like process automation eliminate the uncertainty and inaccuracy of processes. Minimizing the human intervention translates to fewer errors and biases, which in turn mitigates the risk. BPI highlights activities to automate, minimize human error/bias, and add security measures to protect company data.
Regulatory compliance:
Organizations struggle to keep up with compliance regulations that are constantly changing. Business processes need to be flexible enough to adhere to dynamic compliance regulations. Inflexible business processes may result in unforeseen penalties. Documenting compliance-related procedures, policies, and internal controls is a breeze with BPI. Process improvement brings compliance into business processes, creates transparency, and accelerates the implementation of regulatory requirements.
Customer engagement:
Staying ahead of the market and consumer trends is a sure way to build a successful and sustainable business. Upgrading the technology for process improvement accelerates process execution times, which in turn shortens the customer response time. Automating business processes would give employees more time to focus on customer engagement, build proposals, respond to customer requests, and customize solutions.
Technology integration:
Business process improvement methods specify the right software and applications that are best suited for organizational requirements. Seamless technology integration supports businesses with existing and new processes. From employee collaboration to data entry -technology integration benefits organizations across industries.
Agility:
Gaining the competitive edge in your business requires agility and flexibility in business processes. Process improvement tools bring in the agility and flexibility required to adapt to changing market and customer requirements. Business process improvement focuses on implementing flexible processes that can easily adapt to changing business landscapes.
Businesses that decide to implement BPI are often not sure where to start. A comprehensive BPI assessment by way of ROI analysis, onsite audit, and BPI improvement road maps can help businesses decide on the best solutions for greater efficiency and growth.
Automation in Business Process Improvement
Business process automation (BPA) is one of the most popular and simplest ways to improve operational efficiency, eliminate the manual burden, and mitigate process risks. Process automation provides insights for businesses to identify areas of improvement. BPA is part of the business process management methodology that uses software to automate repetitive multi-step business transactions. Most businesses implement BPA as part of their digital transformation to streamline their workflows and improve operational efficiency. BPA is made up of 2 components, namely, automation of process workflows and real-time data management. The conditions that a process must meet to be automated effectively are:
- It should be repetitive by nature
- It should be consistent
- It should not require human intervention
Business process automation is not the same as Industrial automation, the former is a data-driven process improvement technique based on AI, while the latter is software robots that aim at reducing labour. The following steps are to be followed in business process automation:
Identification of repetitive steps to automate: the first step is to identify the repetitive steps that can be effectively automated. Understanding and mapping out the workflow helps identify the steps that can be automated. The decision on which steps to automate must be taken after considering all the factors that affect business performance.
Establishing business goals: once the issues and bottlenecks in the process are identified the next step would be to find the right solution. The new solution must be aligned with the business objectives and overall organizational goals.
Choosing the right workflow automation software: once the end goal is clear, the software for implementing the solution must be chosen. 3 things that must be considered before choosing the software are easy to use and understand interface, flexibility, and integration with existing systems. Cflow from Cavintek is a cloud BPM solution that can be used to automate key business process workflows within minutes. The visual form builder can be used to create tailor-made forms for any business process.
Training the workforce: from the leadership to the employee, everyone needs to understand how the software works and how it would impact/change their work. Successful implementation of the process automation solution requires proactive change management at the organizational level.
Monitoring and tracking performance: the performance of process improvement tools and techniques needs to be reviewed regularly to ensure that the desired goals are met. As the market changes, these tools also need to change to stay relevant.
There are several benefits that businesses can derive from process automation. All the risks associated with manual processes are eliminated by process automation.
Conclusion
Businesses that are flexible, efficient, and responsive to customer and market requirements are the ones that sustain competition. A Mordor Intelligence report on the Global Business Process Management Market reveals that the market is poised to reach 4.28 billion USD by 2026 at a CAGR of 6.26%. Business process improvement is an essential part of the core business strategy.
Building a sustainable business has become synonymous with adopting process improvement methodologies. Lean continuous process improvement methods empower businesses to control costs, improve process efficiencies, and cut out process redundancies. Workflow automation is an effective way of improving process efficiencies. Cflow is an intuitive workflow automation software that is trusted by over 10,000 customers across the globe.
Building automated workflows can be completed within minutes with Cflow. To explore unlimited automation possibilities, sign up for Cflow today.
What should you do next?
Thanks for reading till the end. Here are 3 ways we can help you automate your business:

Do better workflow automation with Cflow
Create workflows with multiple steps, parallel reviewals. auto approvals, public forms, etc. to save time and cost.

Talk to a workflow expert
Get a 30-min. free consultation with our Workflow expert to optimize your daily tasks.

Get smarter with our workflow resources
Explore our workflow automation blogs, ebooks, and other resources to master workflow automation.