Process Improvement Plan with 6 Simple Steps
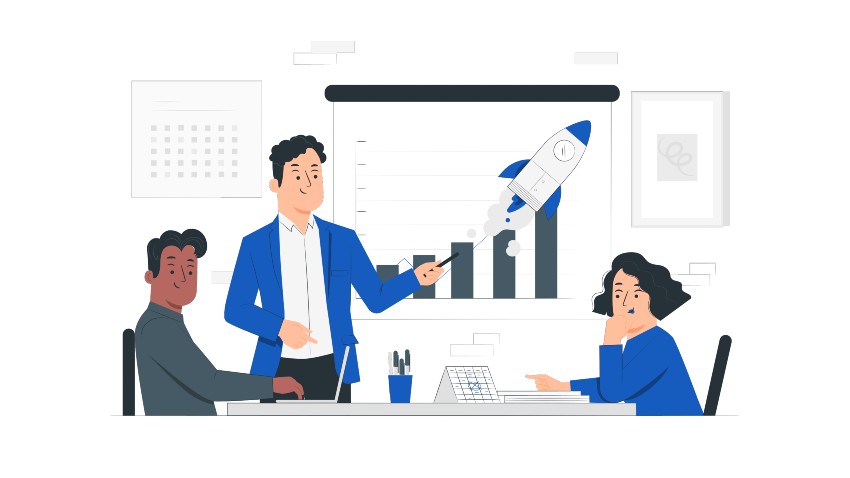
A process is a systematic and well-defined course of action that describes how a set of tasks, communication, and data work together to achieve fixed organizational goals.
These processes need to be optimized regularly to bring out an organization’s maximum efficiency and productivity. But this optimization is not often a simple step to take. Medium and large organizations will undergo a laborious task in detecting the flaw, making the necessary changes, and then finally reorganizing and coordinating a large workforce.
This also demands several rounds of approvals. Hence, a continuous process improvement model is an essential strategy to always ensure the best result. We are going to explore what process improvement plans entail and look into strategies for developing enhanced process improvement plans.
What is a Process Improvement Plan?
A process improvement plan is a set of strategic approaches devised by an organization. This written strategy is to improve the quality of the organizational processes and extract maximum productivity using minimal resources.
Having such a plan will help manage these processes more profoundly. Summing up, a process improvement plan is an official document that defines the improvement strategies of the organizational processes. This includes steps like analyzing and identifying limitations and adopting steps to rectify and improve them.
Benefits of a Process Improvement Plan
The ultimate goal of any organization is to bring out the efficiency in the work that they do. With the rising standards within the industry, organizations will have to constantly meet the expectations of factors like customers, clients, stakeholders, etc. Therefore, consistent improvement has to be achieved to meet the expectations and reach the goals.
For this, a business process improvement plan is always crucial. This strategic plan will act as a framework for your workforce, and make the necessary enhancements to the lacking tasks or areas. The benefits that are acquired with the implementation of a business process improvement plan are as follows:
Improved Engagement and Satisfaction for the Workforce:
With the implementation of a plan, your employees are empowered to work in a healthy environment. If the inefficient processes continue to exist, the workforce’s working proficiency will be disrupted. The tasks have to be optimized so that your employees do not feel like they are performing a mundane activity.
When a well-defined plan is put together, the roles and duties of the employees are specified, and they will be able to plan accordingly. They can effectively work without wasting much time or energy. With increased productivity, the employees will acquire a sense of improvement and accomplishment.
Enhanced Operations:
Undoubtedly, a process improvement plan exists to enhance the organizational processes. When this is achieved, a lot of negatives like wastage of resources, and repetitive and delaying tasks are removed from process workflows. This plan will cleanse your processes making it highly streamlined and beneficial.
Developed Communication:
With a curated plan, the communication system is improved. Communication becomes faster with a system in place and a high level of clarity will be present in the movement of information and other required data. Coordination is automatically established, which further expands the involvement of all the employees who are part of each process.
Increased Innovation:
Establishing a process management plan not only eliminates drawbacks within the processes but simultaneously detects areas of innovation and other additional developmental opportunities.
Heightened Customer Service:
As the overall quality of the processes increases, the output generated is maximized. This will develop the strength of customer service, increasing their satisfaction and creating more probability of customer retention.
Apart from these essential benefits, the following are also achieved that elevate the performance of the business –
- More safety
- Improved productivity
- Streamlined processes
- Increased regulatory compliance standards
- Better customer relationship
- Scope to install feedback systems for employees, customers, and other stakeholders.
Steps in Creating a Process Improvement Plan
Developing process improvement plans for the processes must be performed precisely as they affect the working of your organization. The right strategy must be able to guarantee the most effective results according to your work ethic and culture. Building strategies should have inputs from expert insights and research. For this, an efficient team should be employed. Let us look at the common steps involved in creating a process improvement plan.
1. Employ a Process Improvement Team:
The first step is to create an improvement team to devise the process improvement plan. Having a team will fix the priority of building the right plan for your organization. The team will be responsible for studying the existing processes using a visualization tool like a workflow diagram. They have to analyze each task that goes into different processes and make note of the lacking areas to improvise.
Finally, they have to come up with a process improvement proposal document, which has to be reviewed and approved by the higher officials. On receiving the approval, this business improvement plan will achieve an overall enhancement of the whole process.
2. Choose the Processes to Improve:
Once the team is set up, list down the processes that the team thinks are dragging down the efficiency of the entire process. Identifying the specific factors of the tasks is necessary. For example, it could be the delay that is caused in getting a receipt approved, or in a different case, it could be the case of data handling that has to be manually maintained in a spreadsheet. Such areas need to be pulled out from the process by the team. The team can reach out to employees and stakeholders for feedback that will help them create an optimization plan.
3. Reflect and Identify Issues with the Shortlisted Process:
Once the processes are chosen. A proper study has to be conducted on each of the processes to decide the areas that need optimization. The process has to be studied and analyzed with the existing data.
4. Devise a Strategy for Improving the Process:
When the areas of issues are identified, it is time to develop strategies that could tackle the problems. The improvement team must determine solutions to the issues that come in. These solutions can be anything like eliminating certain activities or shifting to machinery, adopting software tools like automation, artificial intelligence, etc.
5. Test the Strategy:
Before officially launching the strategy on a wider scale, it must be implemented on a smaller scale like a test run, to avoid major losses. During the test run, the performance of the strategy should be noted and measured. This will let you know whether the strategy was a success or not. This will also create opportunities for corrective actions and more improvement. Taking this step will assure your team of success.
6. Implement the Strategy and Optimize:
Once the testing stage is over, the implementation can be done. The multiple rounds of change and updates to your strategy are ready to accomplish the set objectives. When the plan is in action, it is necessary to communicate the objectives and goals to all the involved parties.
What Goes Inside a Business Process Improvement Plan?
Your business process improvement plan must be devised according to your business and its respective goals. The structure of the improvement plan will differ from organization to organization, but there are a few common things that will go into it. Some of these are:
The Process that You Intend to Improve:
The process that you want to improvise will be the primary part of your improvement plan. The plan will contain a description of the organizational process in it.
List of Team Members:
The plan can also list the team members who are working on the optimization of the tasks. Their roles, duties, and responsibilities will be specified clearly to avoid confusion and miscommunication.
Resource Estimation:
The resources can also be listed in a process improvement plan. These resources may include budget, total number of employees, raw materials, etc . Resource planning will guide your planning team to effectively design the process accordingly.
Key Performance Indicators:
Mentioning the KPIs in the improvement strategy is advisable as the employees and stakeholders will be aware of the scale that they are working on. This will help them in monitoring the performance with the KPIs as the criteria. An important point to note here is that different organizations will have their own set of KPIs to achieve.
Recommendations to Consider When Creating the Plan
A change in a system can often be a drastic shift that could alter even the functional structure of any organization. Similarly, when a change is brought into the existing processes, it is essential to consider the following points.
Consistency in Improvement:
Betterment in anything always depends on consistency. Similarly, your improvement plan must be consistent. In a complex process, multiple areas could be lacking without improvement. Therefore, a regular implementation of the process improvement plan is important. To maintain consistency, feedback loops can be placed to get data and information at fixed intervals. Eventually, this revival of your processes will be a part of the business process itself.
Go For the Right Software:
During the plan devising stage, it is convenient if the software is adopted as a channeling platform. This software could help the team members communicate accurately and plan the changes. You can create workflows that would drive coordination among the members. The tool will also document the newly developed process and improve flexibility.
Cflow is one such software solution that will automate most of the repetitive and time-consuming tasks. As a cloud-based tool, documents can be scanned and stored and will also be accessible anytime.
Tips For Using a Process Improvement Plan
While working with the improvement plan, rapport must be brought between all the entities that are working within the system. Therefore, here are some tips to heighten the experience while using the process improvement plan.
1. Communicate with Your Team Members:
In the new system, communication is a crucial element. With proper communication, the efficiency of the work is improved and all the employees can be on the same page till the completion of the process. Collecting feedback is the key. Feedback from multiple ends maintains a level of communication between different entities of your organization. With communication, the plan is also rightly disseminated among all employees.
2. Monitor Results Regularly:
The results of the plan implementation must be monitored at regular intervals. This step will help in constantly detecting issues within the tasks in the processes. Most often, good results may not be achieved right away. You have to be patient with several factors that have to come in line to perform. A key point to note is that it is ideal to have a regular schedule monitoring to check on the progress and suggest corrections when needed.
3. Install Process Management Software:
There are many process management software available in the market. These tools will help you create processes digitally. This software can guide you in having a standardized system where processes and other activities are all optimized and made systematic.
Most Common Types of Process Improvement Plans
There are officially found and established process improvement plan types that most organizations adopt. These different types of plans can be integrated into your organizational process improvement planning. The common types include:
- Six Sigma
- Lean & Lean Six Sigma
- Total Quality Management (TQM)
- Plan-Do-Check-Act (PDCA)
Six Sigma
This process planning method is specific to the quality control developed by a Motorola engineer. The process in the Six Sigma method mainly focuses on five stages, which are DMAIC- define, measure, analyze, improve, and control. The tasks that go under each stage are as follows:
- Define – Project Charter, Customer Input, Value Stream Map
- Measure – Process Map, Capability Analysis, Pareto Chart
- Analyze – Root Cause Analysis, Multi-vari Chart, Failure Mode and Effects Analysis
- Improve – Design of Experiments, Kaizen Event
- Control – Quality Control Plan, 5S Method, Statistical Process Control, Mistake Proofing
This is how a Six Sigma process improvement will take place:
Lean Six Sigma DMAIC Process Flowchart
Lean & Lean Six Sigma
Lean is a method of process improvement that is generally used by manufacturing industries. However, it is essential to note that the principles that this method uses can be adopted across other industries as well. This particular method is adopted to focus on the reduction of waste of resources. This method will help you eradicate tasks or stages within your processes that do not add value to the customers, end users, or the service in general. Five steps are identified in this method. The steps include:
- Identify Value
- Map Value Stream
- Create Flow
- Establish Pull
- Seek Perfection
The Lean & Lean Six Sigma process is a hybrid version of two different methods, Lean and Six Sigma DMAIC, which will guide your organization to achieve the two goals of quality control and waste reduction simultaneously.
Total Quality Management (TQM)
Before the introduction of Lean and Six Sigma approaches, Total Quality Management was one of the most successful methods adopted in the 1980s and the early 1990s. Still, this approach is beneficial and is used even today. Similar to the other two methods, TQM focuses on the quality of the output that is being delivered to the customers. It aims to bring the maximum quality to the process and even higher quality to the final output. TQM holds a set of principles rather than steps. These principles will be taken as a framework that will guide the employees to perform the process improvement plan. These principles include the following:
- Total workforce involvement
- Process-oriented
- Strategic and systematic approach and deliverance
- Continuous
- Data-driven decision-making
- Consistent communication
- Customer-focused
- Complete team integration
Plan-Do-Check-Act (PDCA)
As a continuous change management, Plan-Do-Check-Act (PDCA) was first introduced in the 1950s by W. Edwards Deming, an engineer and management consultant. Initially, it was popularly known as the Deming Wheel. It was later modified and upgraded to the current version by Japanese engineers. The following are the steps involved in the PDCA method.
Plan
- Establish the objectives
- Determine the processes that need to be improvised
Do
- Carry out the set tasks and objectives
Check
- Gather the required data
- Evaluate the results obtained
- Evaluate the testing process
Act
- Implement the improvised process
- Repeat the PDCA cycle regularly to improve performance further
- Standardize instructions and the processes
Examples of Process Improvement Template
After looking at the different types of process improvement methods and types, it is evident that not all organizations have to follow a fixed path for process improvement. Depending on the process type and the organization’s size, affordability, etc. the structure of the plan changes. Each type of improvement plan structure can be taken as a process improvement plan template for you to get started.
These process improvement plan templates can be of different methods as follows:
Method Detailing:
This is a visually appealing template where infographics are used to give the details regarding the improvement method. This template may include details like the method they are adopting and how the method works in a management improvement process, followed by an explanation of all the steps. These can be customized according to the needs of the team or organization.
For example, if an organization has decided to use the PDCA Cycle method to optimize its organizational processes, the following information will be given on the template.
- About the PDCA Cycle
- Examples of where the PDCA Cycle works well
- How the PDCA Cycle works for change management
- Explanation of the steps in PDCA
Problem-Plan Template:
In this template, the problem/issue within the process and the plan of action will be described in detail. This also uses infographics and can be used in cases where the issues are not more than one or two. In this template, the problem will be stated at the beginning, followed by the plan devised by the process improvement team. The plan will entail the corrective measures that have to be taken by the employees.
How does the Process Improvement Plan apply to your Organization?
No organization is an exception to the problems that arise with inefficient business processes. Take any instance like a marketing manager trying to enhance their team’s sales techniques to improve customer conversion rates or the accounts manager trying to bridge the gap in the transaction process; all of these areas can be optimized using a process improvement plan. Adopting this strategy will result in fewer resources, more results, and less time.
Cflow – An Expert in Process Improvement and Management
Cflow is a no-code workflow automation platform that will take your organization’s work experience to the next level of excellence. Our tool easily transforms and streamlines business processes with cloud BPM and workflow automation. This will guarantee you the maximum efficiency of the processes like never before. Every type of organizational need can be met with Cflow. Some important features that we offer are:
- Complete automation of business processes
- Easy workflow creation with zero code involved
- Automated and customized reminders and notifications
- Instant Reports and Analytics
- The approval process made easy and simple
- Encourages integration with third-party applications
Explore more features on Cflow.
Achieving stability and efficiency is not an easy task. With the increasing targets and breakthroughs in the industry, organizations are under constant pressure. To detangle from this scenario, it is essential to optimize your business processes through a process improvement plan. Shifting to this approach will give an end-to-end process improvement, which will enhance the overall performance of your organization. Achieve this success with an expert solution like Cflow. Sign up for a free trial today!