Eliminate Construction Project Delays with Automated Workflows – An Essential Guide
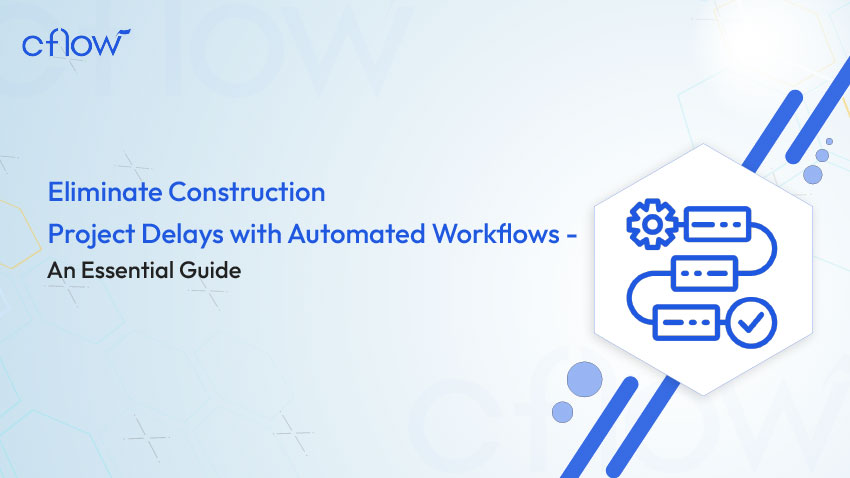
Key takeaways
- Construction delays are a significant contributor to cost overruns in large-scale projects. Studies have shown that large projects typically take 20% longer to finish than scheduled and are up to 80% over budget.
- Construction Workflow Automation enhances scheduling, compliance tracking, and approvals, ensuring smoother project execution and reducing administrative roadblocks.
- AI-driven automation eliminates bottlenecks in procurement and resource allocation, preventing supply chain disruptions that can delay construction timelines.
- Real-time project tracking with workflow automation minimizes risks and improves coordination, ensuring stakeholders stay informed and projects progress without unnecessary delays.
The Financial & Operational Cost of Delays
Delays in construction projects are not just inconvenient—they result in significant financial losses, missed deadlines, and damage to reputation. A significant 85.5% of large-scale construction projects are delivered late, with nearly 23% delayed by over 250 days. A single delayed task can create a domino effect, throwing off schedules, increasing labor costs, and reducing project profitability.
Despite advancements in construction technology, many firms still rely on outdated tracking and approval methods. Manual processes slow down approvals, create scheduling inefficiencies, and lead to material procurement mismanagement.
So, what’s the solution? Automated construction project management. With AI in construction project management, companies can digitize workflows, automate scheduling, and enhance communication to eliminate bottlenecks and keep projects on track.
This blog explores the common causes of construction project delays and how construction scheduling automation improves efficiency. It also provides a step-by-step guide to implementing workflow automation and the best automation tools for construction firms.
Table of Contents
Where Construction Delays Begin: The 5 Hidden Bottlenecks
Construction projects involve multiple moving parts, and delays can stem from various inefficiencies. From approval bottlenecks to material procurement issues, identifying and addressing these challenges is critical to keeping projects on schedule. Below are five major bottlenecks that frequently cause construction delays.
1. Approval Bottlenecks in Project Management
Project approvals for RFIs (Requests for Information), permits, and change orders are essential but often delayed due to manual processing and a lack of centralized tracking. Without an automated system, these approvals get stuck in email threads or paperwork, delaying execution. A slow approval process causes workforce idle time, contract disputes, and project overruns, leading to financial losses.
2. Unoptimized Scheduling & Resource Allocation
Many construction firms still rely on outdated scheduling tools, spreadsheets, or manual tracking, making it difficult to allocate resources effectively. Poor coordination between teams and subcontractors results in unnecessary downtime, workforce inefficiencies, and misaligned task sequencing. The lack of real-time scheduling updates makes it challenging to anticipate delays or make proactive adjustments to workflows.
3. Miscommunication Between Stakeholders
Large construction projects involve multiple stakeholders—contractors, architects, engineers, suppliers, and project managers—who often use different communication platforms. Without a centralized system, real-time updates get lost, causing misalignment in execution. A minor miscommunication can lead to expensive rework, workflow conflicts, and missed deadlines.
4. Material Procurement Delays
Construction materials are essential for smooth project execution, but delays in procurement can bring projects to a standstill. When procurement teams lack predictive tracking or AI-based ordering tools, last-minute shortages lead to costly downtime. Inefficient procurement practices also lead to incorrect material deliveries, excess inventory, or supplier mismanagement, all of which contribute to project overruns.
5. Compliance & Safety Violations Holding Up Work
Regulatory compliance is a major factor in construction, and non-compliance can lead to work stoppages, fines, and legal complications. Tracking safety protocols, inspections, and compliance reports manually increases the risk of missed deadlines due to violations. Failure to adhere to safety standards can also pose risks to worker safety, further extending project completion timelines.
The Role of Automation in Eliminating Construction Delays
The construction industry is increasingly leveraging automation to minimize inefficiencies and streamline project execution. By integrating workflow automation, construction firms can prevent unnecessary delays, reduce risks, and improve overall project efficiency.
According to FlowForma, implementing automation in the construction industry can lead to higher production rates and improved project delivery times. Here’s how automation is reshaping project timelines and operations.
1. AI-Powered Project Scheduling
AI-driven scheduling tools use predictive analytics to optimize task sequencing and ensure that teams remain on schedule. These tools can analyze past project data, anticipate bottlenecks, and suggest real-time adjustments. Automated scheduling workflows send instant updates to project managers, site teams, and contractors, preventing misalignment and scheduling conflicts.
2. Streamlined Approval & Compliance Workflows
Automated Construction Project Management solutions significantly reduce the turnaround time for RFIs, change orders, and compliance documentation. Digital approval workflows route documents to the right decision-makers instantly, eliminating email back-and-forths and paperwork delays. Automated compliance tracking ensures that projects meet regulatory requirements, preventing costly legal issues and safety violations.
3. Centralized Communication Platforms
With a workflow automation system in place, all project communications are consolidated into a single dashboard. Stakeholders receive automated notifications on project updates, upcoming deadlines, and pending approvals, eliminating information silos. This ensures that decision-makers, suppliers, and contractors remain aligned, improving collaboration and reducing miscommunication risks.
4. Predictive Material Procurement
AI-powered procurement forecasting enables teams to order materials in advance, ensuring just-in-time delivery. Automation tools track supplier performance, material availability, and lead times, minimizing procurement-related delays. By analyzing historical data and demand patterns, predictive procurement reduces supply chain disruptions and ensures material readiness before project phases commence.
Implementing Automated Workflows: A Step-by-Step Guide
For major capital expenditure projects, even a 10% overrun can result in a $5 million loss in project profitability. Hence, construction firms looking to streamline operations must approach automation with a clear strategy. The following step-by-step guide outlines how to integrate workflow automation into construction projects for maximum efficiency and minimal delays.
Step 1: Assess the Workflow Bottlenecks in Your Construction Projects
Before implementing automation, conduct a comprehensive audit of your current processes. Identify where delays frequently occur, such as approval wait times, inefficient scheduling, or procurement mismanagement. Understanding the root causes of delays will help define automation priorities and select the right tools for implementation.
Step 2: Select an Industry-Specific Workflow Automation Platform
Not all workflow automation tools are built for construction. Choose an automation solution that integrates with leading construction software such as Procore, Autodesk BIM 360, or Oracle Primavera. Look for platforms that offer:
- Automated approvals and document management to fast-track RFIs, permits, and invoices.
- AI-driven scheduling and forecasting to anticipate delays and optimize workflows.
- Real-time compliance tracking to ensure projects meet industry regulations.
Step 3: Digitize & Standardize Project Approval Processes
Traditional paper-based approvals slow down construction workflows. Transition to digital approval systems where RFIs, permits, change orders, and invoices are routed through an automated workflow. This eliminates bottlenecks and reduces the need for constant follow-ups, ensuring faster project execution.
Step 4: Integrate AI-Based Scheduling & Forecasting Tools
AI-driven scheduling tools use data analytics to predict project completion timelines and detect risks before they escalate. By leveraging predictive models, teams can anticipate scheduling conflicts, workforce shortages, or procurement delays, enabling proactive decision-making.
Step 5: Train Teams & Contractors on the New Workflow System
To ensure smooth adoption, conduct training sessions for project managers, contractors, and site supervisors. Encourage the use of mobile-friendly automation tools so teams can access real-time updates from any location. Proper training ensures that automation benefits are fully realized across all project stakeholders.
Step 6: Monitor & Continuously Optimize Construction Workflows
Workflow automation is an ongoing process. Use AI-driven analytics to measure key performance metrics such as approval turnaround times, material delivery efficiency, and compliance accuracy. Continuously refine workflows based on real-time data to improve project execution and minimize future risks.
Features to Look for in Workflow Automation Solutions for Construction
The construction industry faces numerous workflow challenges, from scheduling conflicts to compliance tracking and resource allocation. Selecting the right construction workflow automation solution ensures projects run smoothly, minimizing inefficiencies and delays. Here are the key features to consider when choosing a workflow automation tool for your construction projects.
1. AI-Powered Scheduling & Forecasting
AI-driven scheduling tools analyze real-time project data, identifying potential bottlenecks and preventing scheduling conflicts. By leveraging machine learning models, these systems optimize task sequencing, ensuring that construction activities follow the most efficient order. Automated scheduling also provides proactive alerts for potential disruptions, allowing project managers to take preventive measures before delays occur.
2. Integration with Construction Management Software
A good workflow automation tool should integrate seamlessly with leading construction management platforms such as Procore, Autodesk BIM 360, and Oracle Primavera. Integration enables a unified approach to tracking project approvals, monitoring compliance requirements, and managing procurement. With a centralized platform, construction teams can coordinate tasks, avoid redundant workflows, and ensure all project-related data is accessible in real-time.
3. Digital Approval & Compliance Tracking
Automating the approval process for permits, RFIs, change orders, and compliance documents eliminates unnecessary delays caused by manual processing. Real-time alerts ensure that projects do not stall due to missing approvals, safety violations, or incomplete regulatory documentation. Workflow automation reduces legal risks, ensuring projects adhere to industry regulations without unnecessary interruptions.
4. Resource Allocation & Workforce Planning
AI-driven workforce scheduling optimizes labor distribution, ensuring that the right personnel are assigned to the right tasks at the right time. Predictive material procurement helps prevent supply shortages by tracking inventory levels and ensuring that materials are ordered proactively. By automating these processes, construction firms can avoid last-minute disruptions and maintain steady project progress.
5. Cloud-Based Project Collaboration
Construction projects involve multiple stakeholders, including project managers, contractors, suppliers, and regulatory authorities. Cloud-based workflow automation tools provide a centralized dashboard where all team members can track progress, monitor task completion, and communicate in real-time. Automated notifications and mobile access ensure seamless coordination, reducing downtime and miscommunication-related delays.
Digital Twin Technology for Construction Project Simulation
The construction industry is increasingly leveraging Digital Twin Technology to enhance project planning, execution, and risk mitigation. A Digital Twin is a real-time virtual representation of a physical construction project, enabling teams to simulate, monitor, and optimize workflows before execution. By integrating Digital Twins with construction workflow automation, firms can significantly reduce project delays, improve efficiency, and minimize costly errors.
How Digital Twins Help Predict and Mitigate Potential Project Delays?
Traditional construction planning often relies on static blueprints and project schedules that fail to account for real-time challenges and environmental variables. Digital Twins offer a dynamic, data-driven model that helps –
- Identify bottlenecks and scheduling conflicts before they impact project timelines.
- Simulate different construction scenarios to optimize task sequencing and resource allocation.
- Monitor equipment and workforce performance in real time to detect inefficiencies early.
- Forecast potential disruptions due to weather conditions, supply chain issues, or labor shortages.
By continuously collecting and analyzing real-time data, Digital Twin technology enhances decision-making, reduces rework, and prevents costly project delays.
Using Real-Time 3D Modeling and Simulation to Optimize Workflows
Digital Twins create interactive 3D models that enable project managers and stakeholders to visualize the construction process before physical work begins. These models integrate with Building Information Modeling (BIM) and AI-powered automation systems to –
- Provide real-time tracking of construction progress through IoT sensors and drones.
- Enable proactive maintenance of machinery by predicting potential failures before they occur.
- Improve safety compliance by simulating risk scenarios and testing safety protocols.
- Enhance team collaboration by providing a shared, up-to-date digital environment for architects, engineers, and contractors.
This level of simulation and analysis minimizes disruptions, ensuring construction projects stay within budget and on schedule.
Integration of Digital Twin Technology with Workflow Automation
When combined with automated construction workflow solutions, Digital Twins unlock new levels of efficiency. Workflow automation tools use AI and predictive analytics to optimize project execution in real-time by –
- Automating approvals for change requests based on real-time site conditions.
- Optimizing material procurement by analyzing demand and supply patterns.
- Coordinating workforce scheduling by tracking on-site activity and reallocating tasks dynamically.
- Improving compliance monitoring through real-time safety inspections and automated reporting.
By bridging the gap between digital modeling and real-world execution, Digital Twin technology and automated construction project management help companies eliminate inefficiencies, reduce project risks, and ensure faster completion of construction projects
End-to-end workflow automation
Build fully-customizable, no code process workflows in a jiffy.
Sustainability & Eco-Friendly Construction Through Automation
Sustainability has become a top priority in the construction industry, with growing emphasis on reducing material waste, optimizing resource efficiency, and lowering carbon emissions. Workflow automation plays a critical role in supporting green building initiatives, ensuring compliance with environmental regulations, and improving energy efficiency in construction projects.
How Workflow Automation Reduces Material Waste and Improves Resource Efficiency
Construction waste accounts for nearly 30% of total building materials used in a project, making it one of the largest contributors to landfill waste. Workflow automation helps reduce this impact by –
- Optimizing procurement processes to ensure only the required amount of materials is ordered, reducing excess waste.
- Tracking material usage in real-time to prevent overuse and improve inventory management.
- Enabling smart scheduling to minimize idle time of machinery and workforce, reducing fuel consumption, and unnecessary emissions.
- Automating construction sequencing to avoid rework and errors, which are major contributors to resource wastage.
With AI-driven construction scheduling automation, firms can implement lean construction principles, ensuring sustainability without compromising efficiency.
How Cflow Powers Workflow Automation in Construction Projects
Efficient construction workflow automation requires a reliable and flexible platform. Cflow is an AI-based, no-code automation solution designed to help construction teams eliminate bottlenecks, streamline approvals, and optimize scheduling. By automating repetitive and time-sensitive tasks, Cflow significantly reduces project delays while enhancing productivity.
Cflow promotes sustainable construction practices by reducing paper-based approvals, minimizing redundant processes, and optimizing resource allocation. By digitizing workflows, Cflow helps construction firms lower their carbon footprint, cut material waste, and enhance energy efficiency across projects.
Key Features of Cflow for Construction Projects –
- Automated Approval Routing – Expedites approvals for RFIs, change orders, and compliance documentation, eliminating administrative bottlenecks.
- AI-Driven Scheduling & Workforce Management – Ensures optimized labor and resource allocation, preventing scheduling conflicts.
- Real-Time Compliance Tracking – Automates regulatory compliance monitoring to prevent violations and legal delays.
- Cloud-Based Collaboration – Provides centralized communication, document sharing, and real-time updates to keep stakeholders aligned.
Cflow’s no-code automation makes it easy for construction firms to set up custom workflows, ensuring greater operational efficiency without complex IT requirements. By integrating AI-driven automation into construction management, companies can complete projects faster, with fewer risks and lower costs.
Conclusion
With construction projects becoming more complex, workflow automation is no longer optional—it’s a necessity. Firms that invest in digital tools and AI-powered solutions can minimize project delays, optimize efficiency, and maintain compliance with ease. AI-driven scheduling, automated approvals, predictive procurement, and real-time tracking can transform construction project management, ensuring timely project completion and cost control.
Sign up for Cflow today and automate your construction workflows with ease!
FAQs
- How does workflow automation reduce construction project delays?
Workflow automation eliminates manual approvals, optimizes scheduling, and improves communication between stakeholders, ensuring projects stay on track. Automated workflows provide real-time progress tracking, predictive analytics for potential bottlenecks, and AI-driven forecasting to help mitigate risks before they escalate. This ensures construction projects are completed on time with fewer disruptions.
- What are the key benefits of automated construction workflows?
Automation ensures faster project execution, cost reduction, improved compliance tracking, and better coordination between contractors, suppliers, and project managers. It also enhances risk management, streamlines document approvals, reduces administrative workload, and prevents supply chain disruptions by enabling predictive procurement and real-time material tracking, keeping the project timeline intact.
- Which construction processes can be automated?
Approval workflows, compliance tracking, scheduling, and procurement management can be automated to enhance efficiency and reduce project delays. Additionally, AI-powered reporting, workforce planning, site safety monitoring, real-time communication between teams, and automated contract and invoice approvals further streamline construction management, improving overall project performance and reducing inefficiencies.
What should you do next?
Thanks for reading till the end. Here are 3 ways we can help you automate your business:

Do better workflow automation with Cflow
Create workflows with multiple steps, parallel reviewals. auto approvals, public forms, etc. to save time and cost.

Talk to a workflow expert
Get a 30-min. free consultation with our Workflow expert to optimize your daily tasks.

Get smarter with our workflow resources
Explore our workflow automation blogs, ebooks, and other resources to master workflow automation.