Definition of Supplier Lifecycle Management
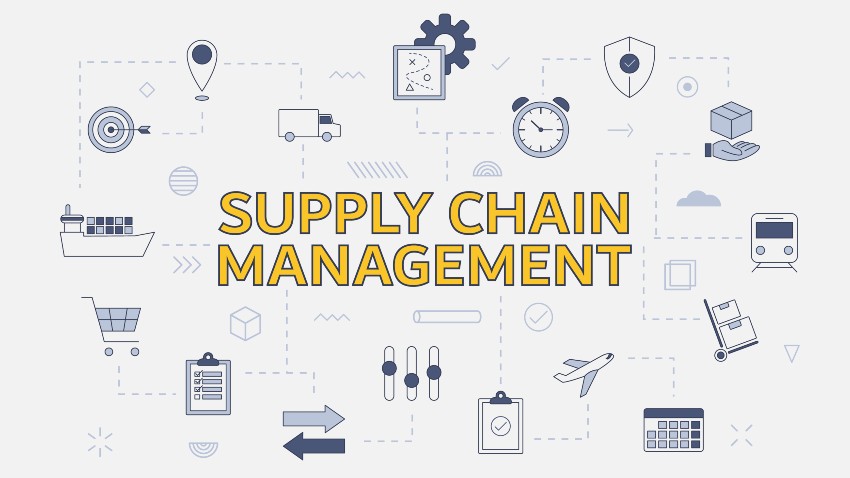
The vendor management lifecycle is an explicit organizational process used for managing external vendors in a well-organized manner. With the changing market conditions, organizations must update their traditional ways of managing vendors to more economical and less risky processes. The vendor management lifecycle process is used to monitor suppliers for their optimal performance, transparency, compliance, and risks throughout their time in the company’s supply chain. Companies with solid vendor management have better control over their supply chains.
This process is sometimes referred to as supplier lifecycle management. Traditionally, the procurement process is broken down into 2 phases: the strategic sourcing process and the transactional or the P2P (purchase-to-pay) process. The strategic sourcing process includes research, supplier selection, and contract management, whereas the P2P process includes requisition, purchasing, and receiving goods and services. In both these phases, the supplier plays a crucial role. This article discusses in detail supplier lifecycle management.
Given the importance of suppliers in the procurement process, it is essential to understand the definition of supplier lifecycle management. Supplier lifecycle management may be defined as the process of managing external vendors in a more transparent and integrated way. Through this process, the company aims to minimize disruptions from external forces since third-party stakeholders are the crucial factors that enhance a company’s supply chain.
What is the Purpose of Supplier Lifecycle Management?
Perhaps the most critical purpose of supplier lifecycle management is to identify the right kind of suppliers and get the best out of them. This needs to be done by ensuring that both cost and risk are minimal, and the quality is maintained throughout the supplier life or the contract period. An organization formulates its supplier lifecycle management through eight unique steps:
- Supplier classification and qualification
- Supplier sourcing evaluation
- Supplier identification and selection
- Supplier onboarding and contract implementation
- Supplier rationalization and performance management
- Supplier risk assessment
- Supplier development and relationship management
- Supplier analysis and reporting.
Procurement and Supplier Lifecycle Management
The process of procurement lifecycle management involves identifying a company’s requirements and selecting a suitable vendor. After selecting the vendor, the company has to negotiate and formulate the contract. After signing the contract, the vendor performance needs to be monitored to ensure the expected services are delivered and the supply chain lifecycle is not interrupted. Finally, the contract needs to be renewed or exited based on the terms and conditions.
Before selecting the vendor, the company must know what the project requires and whether the requirements can be met in-house or by outsourcing from an external supplier. This is the first step in procurement lifecycle management and should be done by the company’s procurement team.
Selecting a vendor can be challenging. Choosing the right vendor ensures that the company’s goals are met and on-time project delivery. Therefore, a company’s procurement team should review potential vendors and narrow down the list. The procurement team can gather details on the vendor’s strengths, weaknesses, and financial stability through a request for information (RFI) from the vendor.
Once the company has selected a vendor, it is important that the procurement team negotiates the contract details and works through the configurable clauses. Both the company and the vendor must agree upon the contract and should feel it is a 100% fit for the company.
Now the company’s project managers monitor the products and services provided by the vendors and check that the services provided comply with company standards. This performance monitoring process continues till the end of the project. The project managers measure the quality and other factors to determine if anything is off the contract’s requirements. The project managers will discuss this with the vendors at the end of the contract.
When the project is completed, the supplier lifecycle comes to an end naturally, and the contract is closed. The procurement activity gets completed once the bills are paid for the services mentioned in the contract. However some contracts may be renewed based on the requirement; for instance, purchasing software for a long term may be renewed outside the project lifecycle for a certain period even after the project ends. This will be handled by the operational team of the company.
SAP Supplier Lifecycle Management
SAP supplier lifecycle management is a holistic approach to vendor relationship management. It helps companies integrate the vendor base as a whole and helps choose the right one from the mix of suppliers. The process involves monitoring individual supplier lifecycles from onboarding to the end of the procurement cycle.
The SAP supplier lifecycle management involves four crucial steps –
- Generating supplier requests
- Registration of suppliers
- Qualification of suppliers
- Approved suppliers
Before formulating the supplier contract, the supplier needs to register their details in the SAP portal and qualify them. Upon successful registration and qualification, the company’s procurement team can make requests based on their requirements. Through the SAP portal only authorized and verified suppliers can contact the company. It is a secure way of choosing the right vendor with minimal risks. Finally, a list of approved suppliers who are in the company’s operational team will handle the company’s favorites based on their past performances and can be made and stored in the portal for using them again in the future.
Benefits of Supplier Lifecycle Management
Before discussing the benefits of supplier lifecycle management, it is essential to discuss its lifecycle. The stages can be easily understood from the supply chain lifecycle diagram shown below:
The above diagram is the integrated representation of the most common phrases in the life of a supply chain. Planning is the imperative step of the supply chain lifecycle, which controls the inventory and development analytics. In the sourcing phase, companies identify the right vendor that is most economical and meets their company standards. The execution phase is planned as per the company’s end product.
The vendor and company need to agree upon the contract’s conditions mutually and deliver what the company needs. Delivery is another crucial step for supply chain management as it directly contributes towards the company’s end product which meets the customers. The product needs to satisfy customers’ expectations. The return phase is the final step of the supply chain lifecycle. It takes place based on the customer’s feedback about the product, and the company decides whether to renew the vendor’s contract.
When a company has a structured approach to supplier lifecycle management, it can reap several benefits.
The first benefit that a company gets from an integrated supplier lifecycle management process is a reduction of process costs. The company’s procurement process can be efficiently enhanced using better planning and low-cost strategies. So, using supplier lifecycle management, the supplier or vendor master data can be easily obtained, including all the necessary details about the vendor that the company needs to determine the supplier’s qualification.
Another crucial benefit is that supplier lifecycle management provides a better understanding of the risks involved with the vendors and helps companies quickly mitigate them. Identifying vendor risk is imperative and needs to be done at the beginning of the procurement process to avoid unnecessary failures and crises.
The best way to manage the distribution lifecycle efficiently is to derive maximum value from supplier capabilities. Managing compliance and ensuring that the supplier contracts are valued, and the company’s financial activities are efficient is vital for the company’s growth. Well-integrated supplier lifecycle management can help manage the compliance, distribution, and performance of the vendors effectively.
Conclusion
Supplier lifecycle management is the heart of the procurement function. According to a recent report, by 2030 supplier lifecycle management is expected to grow by 5.6%, with several supplier lifecycle management software and cost-saving tools poised for market entry. Therefore, understanding the importance of suppliers, their management, and their lifecycle is the first step in improving the efficiency of a company’s procurement function. So, give your company the advantage of no-code workflow automation for an efficient procurement function by signing up for Cflow.