Streamlining Oil and Gas Operations with Automation: Tools, Use Cases, and Key Benefits
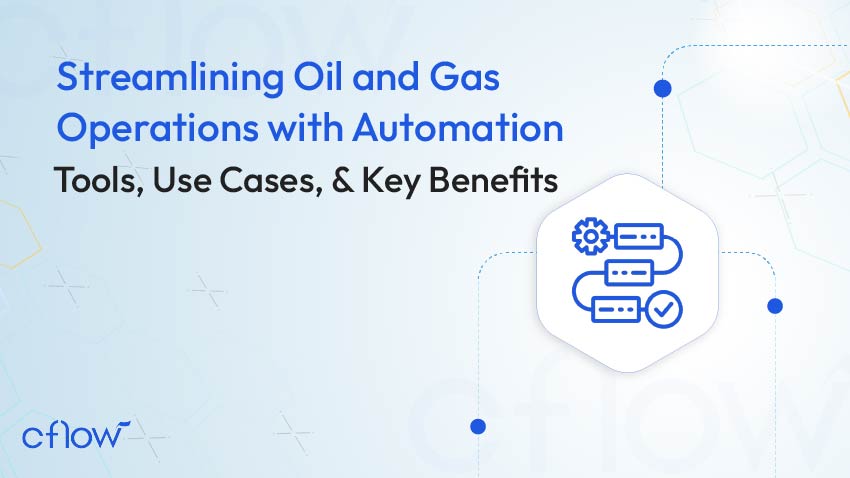
Key takeaways
- Oil and gas automation enhances operational efficiency by enabling real-time monitoring and remote control of critical assets.
- Automation reduces safety risks and downtime through predictive maintenance and process optimization.
- SCADA systems, IoT devices, and AI are transforming upstream, midstream, and downstream operations.
- Companies are adopting automation to improve environmental compliance and reduce costs across drilling and refining processes.
- No-code platforms allow non-technical teams in oil and gas to automate approval workflows without custom coding or IT dependency.
Table of Contents
Introduction to Oil and Gas Automation
Oil and gas automation refers to the integration of digital technologies—such as sensors, control systems, and software—to streamline and optimize various processes across exploration, production, transportation, and refining. The goal is to reduce manual intervention, improve safety, and drive efficiency through data-driven decision-making.
As global energy demand grows, so does the pressure to improve operational output while ensuring safety and sustainability. Automation enables oil and gas companies to monitor remote assets, detect anomalies early, reduce emissions, and optimize asset performance—all in real time.
In this blog, we will explore the components of oil and gas automation, key benefits, common use cases, leading tools, implementation challenges, and how Cflow simplifies automation for the energy sector.
What is Oil and Gas Automation?
Oil and gas automation is the use of control systems, sensors, programmable logic controllers (PLCs), and software to operate and monitor processes with minimal human intervention. These systems are deployed across the oil and gas value chain—from upstream drilling to downstream refining.
At its foundation, oil and gas automation relies on data acquisition, communication networks, and intelligent decision-making frameworks. It brings together hardware and software to create automated responses based on real-time data, enabling operational continuity and responsiveness.
Technologies like SCADA (Supervisory Control and Data Acquisition), DCS (Distributed Control Systems), and RTUs (Remote Terminal Units) are instrumental in collecting and transmitting field data to central control units. These systems allow remote operators to visualize, control, and adjust operations from centralized dashboards.
Automation also incorporates advanced analytics and machine learning to perform predictive maintenance, asset optimization, and safety assurance. By integrating with enterprise systems like ERP or CMMS, automation ensures that operations are not only efficient but also aligned with broader business objectives.
For example, in offshore drilling, automation systems can regulate pump pressure, control mud circulation, monitor equipment integrity, and even halt operations in hazardous conditions, reducing the risk of human error and improving drilling precision.
Need for Automation in the Oil and Gas Industry
The oil and gas industry faces mounting pressure to increase output, improve safety, and reduce operational costs—all while ensuring environmental compliance. Meeting these demands with manual processes alone is no longer feasible. Automation provides a practical solution to manage complex, large-scale operations efficiently and with greater accuracy.
Energy operations often span remote and hazardous environments, such as offshore rigs and high-pressure drilling zones. Automating these processes minimizes the need for on-site human presence, thereby improving safety. Additionally, with real-time monitoring and control, issues can be detected and resolved faster, reducing downtime and costly disruptions.
Another critical driver is the growing demand for data. From pressure readings to flow rates and equipment status, automation systems collect vast amounts of operational data. This data supports predictive maintenance, resource allocation, and strategic planning.
Automation also plays a vital role in regulatory compliance. Environmental regulations require constant monitoring of emissions, leaks, and waste disposal. Automated systems ensure that data is captured continuously, alerts are sent proactively, and reports are generated accurately, ensuring adherence to industry standards.
With shrinking margins and increasing complexity, the need for automation in oil and gas is no longer a choice; it’s a strategic imperative for companies aiming to stay competitive.
Benefits of Automation in Oil and Gas Operations
Automation offers measurable benefits across operational, safety, and environmental domains. As the industry faces increasing pressure to maximize output while reducing risk and cost, automation has emerged as a transformative solution. Here are the expanded benefits:
1. Enhanced Efficiency
Automated systems operate around the clock, reducing downtime and improving consistency. They eliminate process bottlenecks by enabling real-time control over remote assets such as pipelines, compressors, and offshore rigs. Data is collected and acted upon instantly, helping engineers make faster, more accurate decisions.
2. Improved Safety
Automation reduces the need for personnel in dangerous environments, such as high-pressure wells or offshore rigs. Systems can instantly detect gas leaks, pressure fluctuations, or mechanical failures, triggering automatic shutdowns or alerts. This minimizes accidents and enhances worker safety.
3. Cost Optimization
Predictive maintenance powered by automation tools identifies equipment wear and failure risks before they escalate. This prevents unscheduled downtime and avoids costly repairs. In addition, by reducing manual labor requirements, companies can reallocate personnel to higher-value strategic activities.
4. Data Accuracy
Automated data capture reduces human errors and ensures that key operational parameters—such as pressure, flow rate, and temperature—are continuously monitored. Accurate data improves compliance, resource planning, and performance benchmarking across upstream, midstream, and downstream functions.
5. Environmental Monitoring
Automated systems can monitor emissions, detect leaks in real time, and ensure that waste disposal processes comply with environmental laws. This not only supports sustainability goals but also protects companies from regulatory penalties and reputational damage.
Common Use Cases of Automation in Oil and Gas
Automation is applied throughout the oil and gas lifecycle—from exploration to refining—to drive performance, safety, and cost savings. Below are expanded examples that demonstrate how automation supports each phase of the value chain:
Upstream
In exploration and production, automation tools like SCADA systems, IoT-enabled sensors, and AI-driven analytics are used to monitor drilling parameters, optimize hydraulic fracturing, and simulate reservoir performance. Automated rig control systems regulate pressure, rotation, and depth to improve drilling efficiency and safety. Predictive models help forecast reservoir behavior and reduce non-productive time.
Midstream
Pipelines and transport infrastructure are managed using automation for flow rate optimization, temperature and pressure regulation, and leak detection. Remote terminal units (RTUs) collect real-time data and enable centralized control over vast pipeline networks. Compressor stations use automated systems for flow balancing and emergency shutdown procedures, ensuring operational continuity and regulatory compliance.
Downstream
Refineries use Distributed Control Systems (DCS) to automate batch processing, quality assurance, emissions control, and storage logistics. Automation ensures consistent chemical composition, optimizes energy consumption, and alerts operators in case of deviations. Robotics and automated guided vehicles (AGVs) may be used in storage yards and tank farms to manage inventory safely and efficiently.
Compliance and Permit Automation
One emerging use case is automating permit-to-work (PTW) processes. Traditionally handled through paper forms and emails, these permits are now digitized through workflow tools. This enables quicker authorization, reduces operational delays, and ensures full traceability. Automated compliance workflows can route safety documentation, ensure correct sign-offs, and trigger alerts when permits are pending or nearing expiry. This approach enhances workforce accountability while significantly reducing operational risk.
Each of these areas benefits from automation by improving operational visibility, standardizing complex tasks, and enabling data-driven decision-making. Whether it’s reducing equipment wear, enhancing throughput, or maintaining safety protocols, automation transforms how oil and gas companies execute critical operations.
Challenges in Implementing Oil and Gas Automation
Despite its advantages, oil and gas automation comes with challenges that span technical, organizational, and economic domains. Implementing automation requires not only investment in tools and infrastructure but also a cultural and operational shift across departments:
1. Legacy Infrastructure
Many oil and gas facilities rely on legacy systems that lack digital connectivity or real-time capabilities. Retrofitting these systems with automation technologies often requires extensive planning, integration efforts, and budget allocation, particularly when dealing with remote or offshore assets.
2. Cybersecurity Risks
As oil and gas systems become more connected through IoT and cloud-based platforms, they become more exposed to cyber threats. Securing SCADA systems, control networks, and field devices requires a robust cybersecurity strategy, continuous monitoring, and compliance with industry standards like NIST or ISA/IEC 62443.
3. High Initial Investment
Setting up an automated infrastructure often involves high upfront costs, including hardware, software licenses, sensors, and employee training. For smaller or legacy-dependent operators, this can be a significant financial barrier unless phased implementations or ROI-based models are considered.
4. Skill Gaps
The oil and gas workforce is traditionally skilled in mechanical and operational tasks but may lack exposure to digital systems and automation tools. Upskilling employees and hiring automation engineers or data specialists becomes essential to implement and maintain automated systems successfully.
5. Change Resistance
Automation requires a shift in mindset from manual control to digital supervision. Field operators may resist automation due to fear of job loss or unfamiliarity with digital systems. Clear communication, change management programs, and participative training are critical to achieving buy-in and long-term adoption.
Overcoming these challenges requires a structured approach—starting with a clear automation roadmap, executive sponsorship, cross-functional alignment, and the selection of scalable, user-friendly platforms. Building internal capabilities, establishing cybersecurity protocols, and continuously refining workflows are key to long-term automation success.
How Rule-Based Automation Works in Business Processes
At its core, rule-based automation applies conditional logic to data inputs. Rules are created to reflect business logic or compliance requirements. When a trigger event occurs—such as form submission, a deadline, or a change in data—the system checks the rule and initiates an action.
For instance, in a leave approval process, a rule might state: “If leave days requested > 5, route to HR Director for approval.” The system monitors inputs, evaluates conditions, and executes actions like task routing, notifications, or status updates.
This structured flow minimizes ambiguity in decision-making and ensures tasks are consistently processed according to organizational policies.
Benefits of Rule-Based Automation in Finance and HR Workflows
Rule-based automation plays a vital role in automating repetitive tasks in finance and HR departments. In finance, it can enforce rules such as “If expense amount > $5000, escalate to CFO,” ensuring tighter control over high-value approvals. In payroll, rules like “If employee status is ‘contract,’ exclude from monthly bonus” help avoid costly errors.
In HR, onboarding workflows can be streamlined with rules like “If department = IT, assign security access request to IT Admin.” These rules simplify coordination, reduce human oversight, and ensure compliance with internal policies. Additionally, rule-based automation minimizes delays caused by manual routing and follow-ups.
End-to-end workflow automation
Build fully-customizable, no code process workflows in a jiffy.
Top 5 Oil and Gas Automation Tools
Getting approvals for common workflows in oil and gas operations can be challenging when done manually. We have curated a list of no-code workflow automation tools that can simplify and accelerate the approval process in oil and gas.
1. Cflow
Cflow is a no-code automation platform ideal for streamlining workflows across oil and gas operations. It supports conditional logic, rule-based automation, and easy integration with field data systems.
Key Features:
- Visual workflow builder for approvals, inspections, and compliance
- Advanced rules engine for automated routing
- Integration with ERP and SCADA systems
- Role-based access and mobile-friendly dashboards
- Custom form builder for field data collection
Pricing:
- Happy Plan: $7/user/month
- Joy Plan: $11/user/month
- Bliss Plan: $16/user/month
2. AVEVA System Platform
AVEVA provides a comprehensive industrial automation solution for SCADA, HMI, and operations management.
Key Features:
- Unified operations control across drilling, production, and refining
- SCADA visualization and data modeling
- Real-time alarm management
- Analytics and predictive insights
Pricing:
- Custom pricing based on deployment scope
3. Siemens SIMATIC PCS 7
Siemens offers an advanced DCS tailored to the needs of oil and gas processing plants.
Key Features:
- Scalable process automation architecture
- Batch and continuous processing control
- Fail-safe operation in hazardous areas
- Integrated engineering tools for system maintenance
Pricing:
- Custom pricing (enterprise-level solution)
4. Honeywell Experion PKS
Honeywell’s automation suite enables remote control and performance optimization for the oil and gas value chain.
Key Features:
- Unified platform for control and safety systems
- Asset management and equipment diagnostics
- Cybersecurity hardening tools
- Real-time operational intelligence
Pricing:
- Quoted per project
5. Rockwell Automation FactoryTalk
Rockwell Automation offers industrial automation tools designed for high-reliability environments.
Key Features:
- Plant-wide control and monitoring
- Energy efficiency analytics
- Edge-to-cloud connectivity
- Modular architecture for upstream and midstream
Pricing:
- Tiered pricing based on the license model
Key Trends in the Oil and Gas Industry
The oil and gas sector is evolving rapidly, with automation acting as a key driver of transformation. Here are some of the leading trends shaping automation in this industry:
- Digital Twin Technology: More companies are adopting digital twins to simulate drilling operations, predict maintenance needs, and optimize production planning. These virtual replicas provide real-time feedback for faster, safer decision-making.
- Edge Computing: With operations often located in remote areas, edge computing allows data processing to occur on-site, reducing latency and enabling immediate responses to operational changes.
- AI and Predictive Analytics: Artificial intelligence is increasingly used to detect patterns in equipment performance and predict failures before they happen, thus minimizing downtime and extending asset life.
- Cloud-Based SCADA Systems: Traditional on-premise SCADA systems are giving way to cloud-based platforms that offer better scalability, remote access, and integration with enterprise tools.
- Focus on ESG Compliance: Automation now plays a crucial role in helping companies meet environmental, social, and governance (ESG) requirements. From emissions tracking to digital safety records, automation supports more transparent and auditable operations.
These trends highlight a clear direction: oil and gas companies are embracing smarter, more connected systems that support safety, compliance, and efficiency at scale.
How Cflow Supports Oil and Gas Automation
Cflow enables energy companies to implement automation without writing code. Getting approval for some of the oil and gas operations can be a burden for the admin teams, especially when they follow manual methods. Cflow can simplify this process by automating these repetitive and mundane steps with no-code AI-powered workflows.
Whether managing field inspections, maintenance schedules, or health and safety workflows, Cflow helps standardize operations and minimize manual intervention. It adapts easily to fluctuating project scopes and integrates with industry-standard platforms, enabling centralized monitoring and management.
Key Capabilities of Cflow for the Oil and Gas Sector
Visual Workflow Builder
Create, deploy, and manage automated workflows for field operations, approvals, safety documentation, and regulatory reporting—all using an intuitive drag-and-drop interface.
Advanced Rules Engine
Define complex logic such as conditional task routing, automatic approvals, deadline-based alerts, and escalation paths. For example, “If inspection form = incomplete AND risk level = high, escalate to site supervisor.”
Integration with Industry Tools
Cflow integrates seamlessly with SCADA systems, email, ERPs, and document repositories, enabling real-time data exchange and end-to-end process automation.
Field-Friendly Mobile Access
Technicians and supervisors can initiate, update, or approve workflows directly from the field using Cflow’s mobile-friendly interface, reducing delays and improving data accuracy.
Compliance Automation
Automate safety checklists, permit-to-work (PTW) workflows, and incident reporting. Cflow ensures all compliance records are logged, traceable, and audit-ready.
Performance Monitoring and Analytics
Visual dashboards and reports provide insights into workflow performance, task bottlenecks, and SLA breaches, helping leadership drive continuous improvement.
Role-Based Access and Security
Ensure data integrity with customized access control and secure handling of operational and compliance documents.
Cflow empowers oil and gas teams to digitize manual workflows, enhance field coordination, and maintain compliance—all without heavy IT overhead. Its flexible architecture and rule-driven automation are built to meet the complex, high-stakes demands of the energy industry.
Final Thoughts
Oil and gas automation is no longer optional—it has become a strategic priority for companies aiming to remain competitive, safe, and compliant in an increasingly complex energy landscape. As the demand for energy rises and pressure mounts to improve sustainability, automation provides the tools to meet these expectations without compromising safety or efficiency.
By automating routine operations, organizations can reduce downtime, detect anomalies early, and ensure consistent process execution across vast geographical operations. Whether it’s remote well monitoring or permit-to-work compliance, automation unlocks new levels of agility and responsiveness.
The transition toward digital workflows also fosters better collaboration across departments and geographies, allowing companies to share insights, report faster, and respond more effectively to disruptions. With increasing emphasis on ESG goals, automation supports accurate tracking and transparent reporting of environmental and safety metrics.
Platforms like Cflow enable this transformation without adding IT burden, thanks to its no-code environment, flexible rule engine, and broad integration capabilities. Cflow empowers both field operators and decision-makers with intuitive tools that drive real business outcomes.
Now is the time to digitize and automate your oil and gas operations. Sign up for Cflow today to experience a smarter, safer, and more efficient way of working.
FAQs
What is oil and gas automation?
Oil and gas automation is the use of digital systems and software to control and monitor field and plant operations with minimal human intervention.
How does automation improve safety in oil and gas?
Automation reduces the need for workers in hazardous areas and enables real-time monitoring, early warning systems, and automated shutdowns in case of anomalies.
Which processes are commonly automated in oil and gas?
Commonly automated processes include drilling operations, well monitoring, pipeline control, equipment diagnostics, and refinery management.
Can smaller oil companies afford automation?
Yes. No-code platforms like Cflow offer cost-effective automation solutions that are scalable and accessible to small and mid-sized operations.
Is cybersecurity a concern in oil and gas automation?
Yes. As automation increases connectivity, strong cybersecurity frameworks are essential to protect critical infrastructure from cyber threats.
What should you do next?
Thanks for reading till the end. Here are 3 ways we can help you automate your business:

Do better workflow automation with Cflow
Create workflows with multiple steps, parallel reviewals. auto approvals, public forms, etc. to save time and cost.

Talk to a workflow expert
Get a 30-min. free consultation with our Workflow expert to optimize your daily tasks.

Get smarter with our workflow resources
Explore our workflow automation blogs, ebooks, and other resources to master workflow automation.