- Cflow
- Quality Control Sign-Off Automation
Quality Control Sign-Off Automation

Clow Team
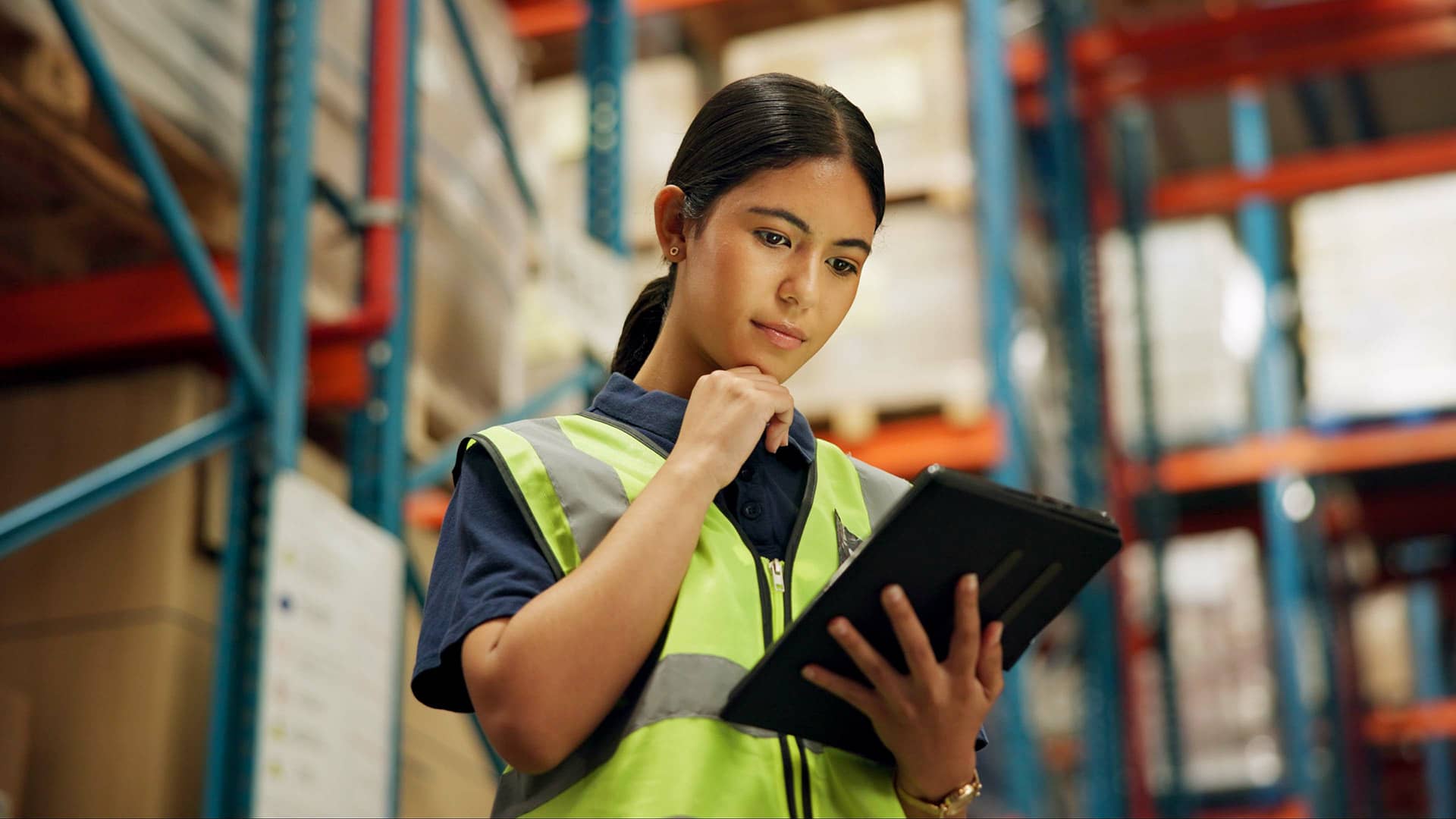
Quality Control (QC) sign-offs ensure that products, components, and processes meet defined specifications before release or handoff to the next stage. Without automation, manual QC approvals lead to delays, inconsistent inspections, regulatory risks, and costly rework. Recent industry research shows that 57% of manufacturing companies experience production delays due to slow or inconsistent QC approvals.
Without automation, quality inspectors, production supervisors, compliance officers, and plant managers struggle to coordinate inspections, enforce QC standards, track approvals, and maintain audit trails. This guide walks you through exactly how Cflow automates Quality Control Sign-Off Process, from inspection submission to final product release.
What Is Quality Control Sign-Off Process?
The Quality Control Sign-Off Process governs how quality inspections are documented, reviewed, and approved before products are cleared for shipment, assembly, or next-stage processing while ensuring compliance with quality and regulatory standards.
Think of QC sign-offs like safety checkpoints , every inspection requires specification validation, documentation review, multi-level approvals, and traceable sign-off before products move forward.
Recent industry research shows that automating QC sign-offs reduces defect rates by 40% and shortens inspection cycles by 55%.
Why Quality Control Sign-Off Matters for Organizations
Product Quality Assurance
Compliance Readiness
Production Efficiency
Audit Trail
Try Cflow for free, no credit card needed
Key Benefits of Automating Quality Control Sign-Off with Cflow
- Centralized QC Inspection Portal : Cflow allows quality teams to submit inspection reports, measurement data, defect logs, and photos into a single, trackable workflow.
- Dynamic Routing Based on Inspection Results : Cflow applies routing logic based on defect severity, product type, and compliance category.
- Multi-Level Approval Workflows : Inspections route through quality leads, production supervisors, compliance officers, and plant managers depending on inspection outcome.
- Real-Time Notifications & Escalations : Automated alerts ensure timely inspection reviews while escalation rules prevent production holds.
- Defect Categorization & Rework Triggers : Cflow flags critical defects automatically, assigns corrective action tasks, and blocks further processing until issues are resolved.
- Full Audit Trail & Compliance Logs : Every inspection result, approval, defect correction, and release is archived for regulatory audits.
- Mobile Accessibility : Quality inspectors and supervisors can perform inspections, capture data, and approve sign-offs on mobile devices.
Get the best value for money with Cflow
User Roles & Permissions
Quality Inspector (Initiator)
- Responsibilities: Conduct inspections, record measurements, capture defect data, and submit for review.
- Cflow Permission Level: Submit Form.
- Mapping: “Quality Group.”
Quality Supervisor
- Responsibilities: Validate inspection reports, approve compliant items, and escalate nonconformities.
- Cflow Permission Level: Approve/Reject.
- Mapping: “QC Supervisor Group.”
Compliance Officer
- Responsibilities: Verify regulatory compliance for flagged issues and ensure documentation is complete.
- Cflow Permission Level: Approve/Reject.
- Mapping: “Compliance Group.”
Production Manager
- Responsibilities: Confirm production readiness for approved batches and schedule rework for rejected items.
- Cflow Permission Level: Approve/Reject.
- Mapping: “Production Group.”
Plant Manager (Conditional)
- Responsibilities: Final sign-off for critical batches or escalated issues.
- Cflow Permission Level: Approve/Reject.
- Mapping: “Plant Leadership.”
Discover why teams choose Cflow
Form Design & Field Definitions
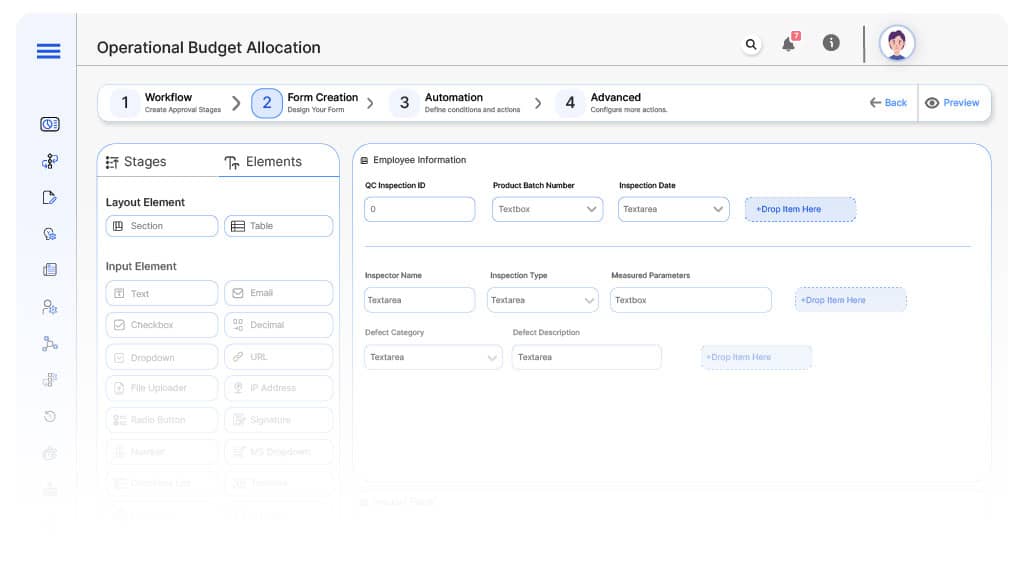
Field Label: QC Inspection ID
- Type: Autonumber
- Auto-Populate: Generated on submission.
Field Label: Product Batch Number
- Type: Text
- Logic/Rules: Mandatory.
Field Label: Inspection Date
- Type: Date Picker
- Logic/Rules: Mandatory.
Field Label: Inspector Name
- Type: Text (Autofill)
- Auto-Populate: From user profile.
Field Label: Inspection Type
- Type: Dropdown (Incoming, In-Process, Final, Pre-Shipment)
- Logic/Rules: Drives routing.
Field Label: Measured Parameters
- Type: Repeater (Parameter Name, Spec Limit, Actual Value)
- Logic/Rules: Mandatory.
Field Label: Defect Category
- Type: Dropdown (Critical, Major, Minor, None)
- Logic/Rules: Drives routing.
Field Label: Defect Description
- Type: Text Area
- Logic/Rules: Mandatory if any defect is recorded.
Field Label: Inspection Photos
- Type: File Upload
- Logic/Rules: Optional.
Field Label: Corrective Action Required
- Type: Checkbox
- Logic/Rules: Checked for Critical or Major defects.
Field Label: Supervisor Review Notes
- Type: Text Area
- Logic/Rules: Required for QC Supervisor.
Field Label: Compliance Review Notes
- Type: Text Area
- Logic/Rules: Required for Production Manager.
Field Label: Plant Manager Comments
- Type: Text Area
- Logic/Rules: Required for Plant Manager.
Field Label: Release Confirmation
- Type: Checkbox
- Logic/Rules: Marks product released.
Transform your Workflow with AI fusion
Approval Flow & Routing Logic
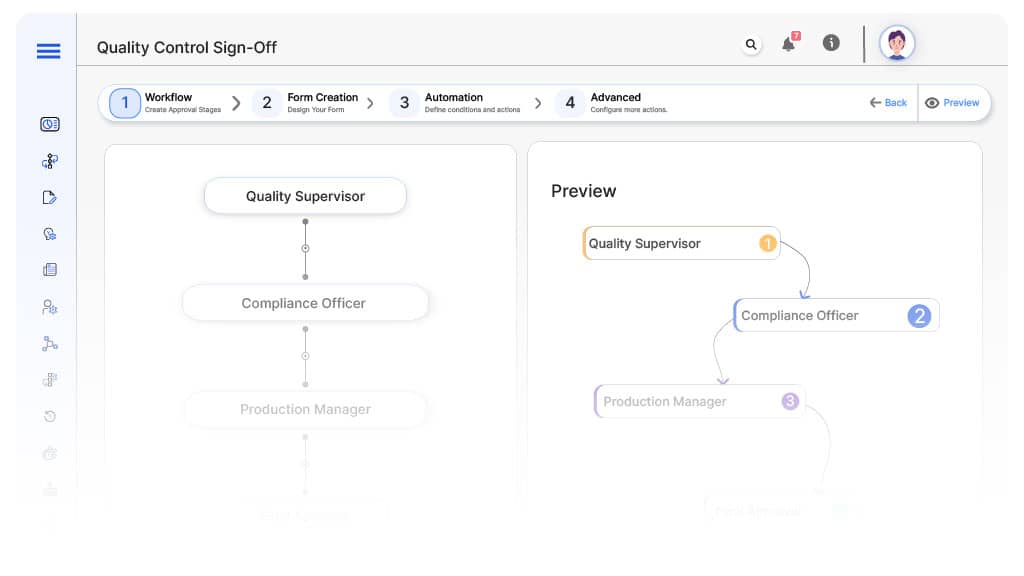
Submission → Quality Supervisor
- Status Name: Pending QC Supervisor Review
- Notification Template: “Hi QC Supervisor, new inspection submitted for review.”
- On Approve: Moves to Compliance (if applicable).
- On Reject: Returns to Inspector.
- Escalation: Reminder after 1 day.
QC Supervisor → Compliance Officer (Conditional)
- Condition: If Critical or Major defects present.
- Status Name: Pending Compliance Review
- Notification Template: “Hi Compliance, inspection flagged for regulatory review.”
- On Approve: Moves to Production Manager.
- On Reject: Returns to QC Supervisor.
- Escalation: Reminder after 1 day.
Compliance → Production Manager
- Status Name: Pending Production Review
- Notification Template: “Hi Production, batch ready for release or rework planning.”
- On Approve: Moves to Plant Manager (if applicable).
- On Reject: Returns to Compliance Officer.
- Escalation: Reminder after 1 day.
Production → Plant Manager (Conditional)
- Condition: High-risk or strategic production batches.
- Status Name: Pending Plant Manager Review
- Notification Template: “Hi Plant Manager, final batch sign-off required.”
- On Approve: Moves to Release Authorized.
- On Reject: Returns to Production Manager.
- Escalation: Reminder after 1 day.
Final → Release Authorized
- Status Name: Batch Approved & Released
- Notification Template: “Batch fully approved and released for next stage.”
Transform your AI-powered approvals
Implementation Steps in Cflow
Create a new workflow
Design the form
Set up User Roles/Groups
Build the process flow diagram
Configure notifications
Apply templates and escalation rules per Approval Flow.
Set conditional logic
Save and publish workflow
Activate process.
Test with a sample request
Adjust logic if needed
Go live
Example Journey: Medical Device Inspection
FAQ's
Setup typically completes within 5–7 business days.
Unleash the full potential of your AI-powered Workflow
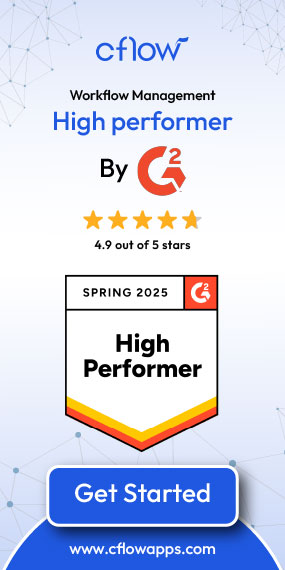